1. 서 론
2. 계획법 선정 및 분석 방법
2.1 실험계획법 선정
2.2 입력인자, 출력인자 설정
2.3 데이터 수집 및 수준 설정
3. 수집데이터 분석 및 기여도 확인
3.1 입력인자와 출력인자의 상관관계 확인
3.2 기여도 분석
4. 결 론
1. 서 론
발파 공법을 이용하여 도심지 굴착 시 소음에 관련된 민원이 자주 발생함에 따라 기계식 굴착의 필요성이 증가되고 있다. 기계식 굴착이란 로드헤더, TBM과 같은 기계장비를 이용하여 굴착하는 것으로 진동과 소음이 적어 민원을 최소화할 수 있다. 기계식 굴착 장비 중 하나인 로드헤더의 굴진율에 대해서도 많은 연구가 이루어지고 있다. 암석의 일축압축강도를 이용하여 기계장비의 굴진율을 예측하는 방법이 먼저 제안되었으며(Thuro and Plinninger, 1998 and 1999, Restner and Plinninger, 2015, Bilgin et al., 1996), 그 이후 절삭 간격과 절삭 깊이의 비에 따라 비에너지를 주요 인자로 굴진율을 추론하는 연구도 진행된 바 있다(Bilgin et al., 2005, Rostami et al., 1994 and 2011). 이들 선행연구는 굴진율과 직접적인 연관이 있는 1개, 혹은 2개의 변수를 선택한 후 로드헤더의 굴진율을 예측하는 모델을 제시하고 있다.
실제 터널굴진 환경에서는 다양한 인자가 로드헤더의 굴진율에 영향을 미친다. 굴진대상 암반의 조건, 장비의 성능, 커팅헤드 설계값, 운용 조건들이 복합적으로 작용하여 절삭깊이, 절삭력 등이 1차적으로 결정된다. 이러한 결정인자들은 다시 장비전체의 성능과 굴진율에 추가적인 영향을 미친다. 본 기술보고는 이들 입력인자와 1차 결정인자 사이의 상관관계를 분석하고자 하였다. 우선 로드헤더의 픽커터 절삭시험을 수행한 선행 연구사례를 수집하였다. 연구사례의 데이터를 취합 후, 입력 인자와 출력 인자로 분류한 후, 가상의 실험계획을 수립하였다. 그리고 실험계획의 결과를 임의로 도출한 후, 출력 인자에 대한 입력 인자의 기여도를 분산분석(ANOVA, analysis of variance)을 통해 조사했다. 이를 통해 로드헤더의 운영조건이나 암반의 조건이 로드헤더의 굴진 시 미치는 기여도를 조사하였다.
2. 계획법 선정 및 분석 방법
2.1 실험계획법 선정
실험계획법(Design of experiment)이란 입력 변수들을 조작하여 출력 변수들에 미치는 효과를 보는 방법이다. 실험계획법은 요소별, 목적별, 인자별로 다양한 방법이 있으며, 본 기술보고에서는 다구찌 직교배열표를 채택하여(Taguchi and Phadke, 1989) 실험계획법을 작성 후, 통계학적 분석법인 분산분석을 통해 각 출력변수에 대한 입력변수의 기여도를 분석하였다. 다구찌 방법은 직교배열표를 이용하며 완전요인배치법에 비해 적은 횟수로 실험의 계획이 가능하다. 실험기간을 줄이는 데 효과적이며 직교배열표의 교호작용에 신경 쓰지 않아도 된다. 또한 실험 데이터로부터 분산분석 데이터를 추출하기 수월하다.
2.2 입력인자, 출력인자 설정
입력 인자는 암반의 물성 인자와, 로드헤더의 운영, 설계 인자로 분류했다. 암반의 입력 인자는 암석의 강도와 로드헤더 굴진율의 상관관계를 제시한 논문(Thuro and Plinninger, 1998, Restner and Plinninger, 2015)을 참조하여 암석의 일축압축강도(UCS, uniaxial compressive strength)로 설정했다(Fig. 1). 로드헤더의 입력 및 설계 관련된 입력 인자는 절삭 깊이(depth, cutting depth), 절삭 간격(spacing, cutting spacing), 받음각(attack angle), 비틀림각(skew angle)으로 설정했다. 출력 인자는 로드헤더로 암석 절삭 시 얻어지는 비에너지(SE, specific energy), 평균 절삭력(mean cutting force), 최대 절삭력(peak cutting force), 평균 수직력(mean normal force), 최대 수직력(peak normal force)으로 설정했다.
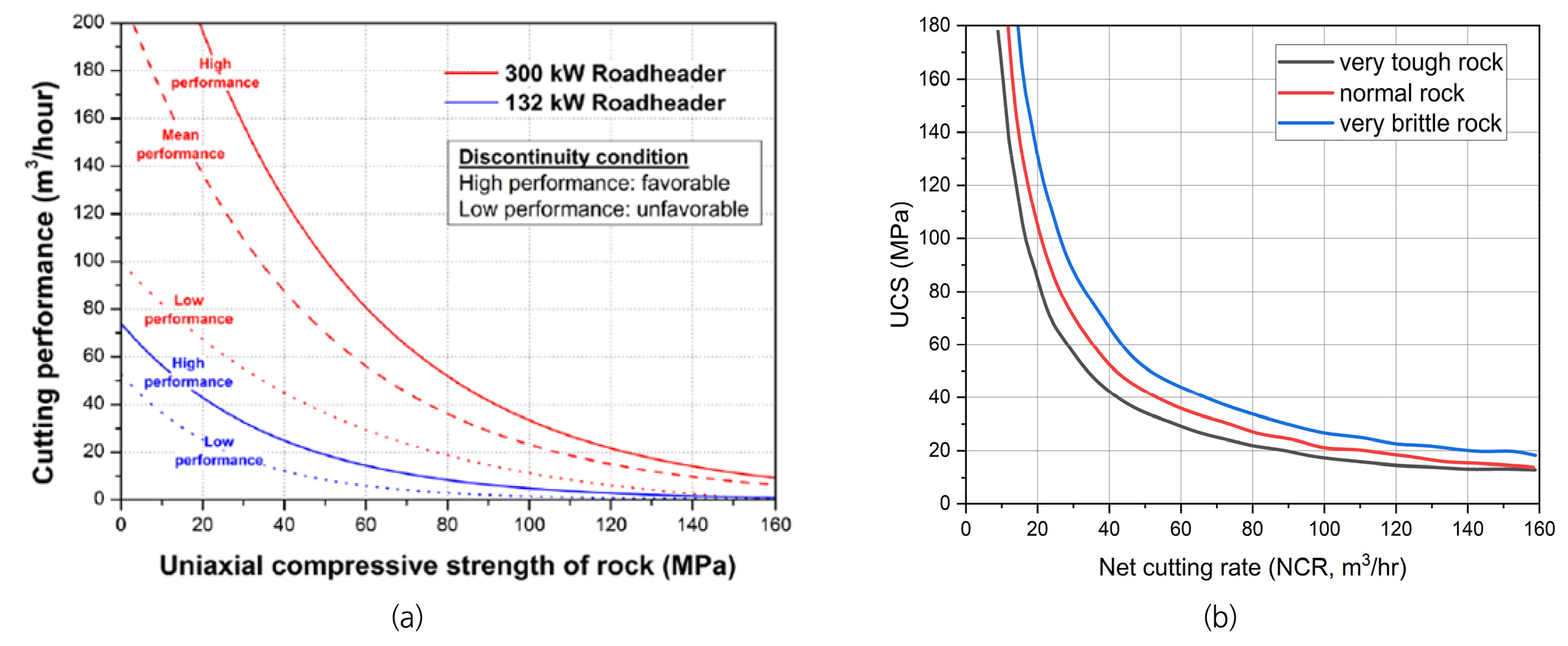
Fig. 1.
2.3 데이터 수집 및 수준 설정
설정한 입력 인자와 출력 인자가 모두 들어있는 논문들의 데이터를 Table 1에 취합하였다(Bilgin et al., 2006, Wang et al., 2017, Park et al., 2018, Jeong et al., 2020). 입력 인자는 일축압축강도, 절삭 깊이, 받음각, 비틀림각, 절삭 간격 5가지이다. 입력 인자들의 수준을 설정하기 위해 취합한 데이터에 맞는 5요인에 대한 직교배열표를 찾았다. 절삭 간격이 다른 입력 인자에 비해 넓은 분포를 가지고 있어 혼합 수준 직교 배열표를 다구찌 기법으로 설계하였다. 절삭 간격은 상대적으로 넓은 범위의 실험조건이 검색되어 6수준으로 설정했으며, 일축압축강도, 절삭 깊이, 받음각, 비틀림각은 3수준으로 설정했다. 그에 따른 출력인자는 비에너지, 평균절삭력, 최대 절삭력, 평균 수직력, 최대 수직력으로 설정하였다. 그 후 데이터를 기입하여 직교배열표를 완성하였다(Table 2). 선행 문헌마다 사용한 픽의 크기나 형상이 다를 수 있지만, 커터의 형상은 본 연구에서 고려하지 않았다.
Table 1.
Summarized data of rock cutting for pick cutters
UCS
(MPa)
|
Depth
(mm)
|
Spacing
(mm)
|
Attack
angle (°)
|
Skew
angle (°)
|
SE
(MJ/m3)
|
Mean
cutting
force
(kN)
|
Peak
cutting
force
(kN)
|
Mean
normal
force
(kN)
|
Peak
normal
force
(kN)
|
17.9
|
3
|
6.0
|
55
|
0
|
3.38
|
0.18
|
0.33
|
0.22
|
0.34
|
17.9
|
3
|
9.0
|
55
|
0
|
2.99
|
0.27
|
0.56
|
0.31
|
0.58
|
17.9
|
3
|
12.0
|
55
|
0
|
3.90
|
0.46
|
0.81
|
0.48
|
0.76
|
79.2
|
6
|
9.0
|
55
|
0
|
8.67
|
0.98
|
2.18
|
1.09
|
1.94
|
79.2
|
6
|
12.0
|
55
|
0
|
7.43
|
1.41
|
3.25
|
1.52
|
2.65
|
79.2
|
6
|
18.0
|
55
|
0
|
7.66
|
2.21
|
4.92
|
2.53
|
4.29
|
38.0
|
9
|
27.0
|
55
|
0
|
21.8
|
6.96
|
19.8
|
6.31
|
16.8
|
30.0
|
9
|
27.0
|
55
|
0
|
9.62
|
4.12
|
12.0
|
3.12
|
9.29
|
64.0
|
5
|
5.0
|
45
|
0
|
83.0
|
3.21
|
7.64
|
3.61
|
8.95
|
64.0
|
5
|
10.0
|
45
|
0
|
77.7
|
4.25
|
10.1
|
4.38
|
10.1
|
64.0
|
5
|
15.0
|
45
|
0
|
77.9
|
5.21
|
13.2
|
5.29
|
13.3
|
64.0
|
5
|
20.0
|
45
|
0
|
67.6
|
5.81
|
13.0
|
5.87
|
13.5
|
21.0
|
4
|
12.0
|
45
|
0
|
23.0
|
0.96
|
1.80
|
1.20
|
2.25
|
21.0
|
4
|
16.0
|
45
|
0
|
24.7
|
1.10
|
2.02
|
1.27
|
2.34
|
21.0
|
4
|
20.0
|
45
|
0
|
31.6
|
1.29
|
2.30
|
1.60
|
2.73
|
21.0
|
6
|
6.0
|
45
|
0
|
41.2
|
1.08
|
2.33
|
1.48
|
3.10
|
21.0
|
6
|
12.0
|
45
|
0
|
22.4
|
1.32
|
2.36
|
1.77
|
3.04
|
Table 2.
Data arranged in an orthogonal array table
No.
|
Spacing
(mm)
|
Depth
(mm)
|
Attack
angle (°)
|
Skew
angle (°)
|
UCS
(MPa)
|
SE
(MJ/m3)
|
Mean
cutting
force
(kN)
|
Peak
cutting
force
(kN)
|
Mean
normal
force
(kN)
|
Peak
normal
force
(kN)
|
1
|
6.0
|
4.0
|
45
|
-12.5
|
19
|
44.0
|
0.86
|
1.61
|
1.14
|
2.03
|
2
|
6.0
|
7.0
|
55
|
0.0
|
48
|
60.3
|
1.43
|
3.28
|
1.45
|
3.28
|
3
|
6.0
|
11.5
|
60
|
12.5
|
72
|
88.1
|
2.23
|
4.85
|
2.17
|
4.76
|
4
|
11.5
|
4.0
|
45
|
0.0
|
48
|
37.2
|
2.21
|
4.64
|
2.29
|
4.68
|
5
|
11.5
|
7.0
|
55
|
12.5
|
72
|
8.05
|
1.20
|
2.71
|
1.31
|
2.29
|
6
|
11.5
|
11.5
|
60
|
-12.5
|
19
|
46.3
|
6.97
|
16.1
|
7.29
|
17.2
|
7
|
17.5
|
4.0
|
55
|
-12.5
|
72
|
62.8
|
6.06
|
14.4
|
5.67
|
13.9
|
8
|
17.5
|
7.0
|
60
|
0.0
|
19
|
22.1
|
0.99
|
2.04
|
0.99
|
2.11
|
9
|
17.5
|
11.5
|
45
|
12.5
|
48
|
37.7
|
6.63
|
19.2
|
7.96
|
19.5
|
10
|
24.0
|
4.0
|
60
|
12.5
|
48
|
42.2
|
6.07
|
11.8
|
6.84
|
12.8
|
11
|
24.0
|
7.0
|
45
|
-12.5
|
72
|
62.9
|
8.63
|
23.9
|
5.88
|
19.4
|
12
|
24.0
|
11.5
|
55
|
0.0
|
19
|
18.1
|
1.86
|
3.39
|
2.30
|
4.09
|
13
|
32.0
|
4.0
|
55
|
12.5
|
19
|
1.12
|
1.82
|
1.08
|
1.41
|
24.1
|
14
|
32.0
|
7.0
|
60
|
-12.5
|
48
|
5.94
|
3.40
|
8.38
|
3.55
|
6.13
|
15
|
32.0
|
11.5
|
45
|
0.0
|
72
|
37.9
|
11.3
|
31.9
|
8.33
|
27.5
|
16
|
46.0
|
4.0
|
60
|
0.0
|
72
|
32.7
|
10.0
|
24.9
|
13.0
|
27.9
|
17
|
46.0
|
7.0
|
45
|
12.5
|
19
|
3.81
|
1.93
|
3.41
|
1.81
|
2.74
|
18
|
46.0
|
11.5
|
55
|
-12.5
|
48
|
7.14
|
3.75
|
9.40
|
3.79
|
6.49
|
3. 수집데이터 분석 및 기여도 확인
3.1 입력인자와 출력인자의 상관관계 확인
기여도 분석을 하기 전 수집한 데이터들을 사용하여(Table 1) 실험계획법에서 설정한 입력인자와 출력인자 간 상관관계가 있는지 확인하였다. 데이터 간의 상관관계를 선형적으로 회귀한 문헌이 많았기 때문에(Bilgin et al., 2006, Wang et al., 2017), 본 기술보고의 입력인자와 출력인자로 설정한 인자들의 상관관계를 선형회귀분석을 진행하여 그래프로 나타냈다(Figs. 2, 3, 4, 5, 6, 7).
출력인자인 비에너지(SE), 절삭력(cutting force), 수직력(normal force)과 입력인자인 절삭 깊이(depth), 절삭 간격(spacing), 일축압축강도(UCS)의 관계 대해 분석하였다. 받음각과 비틀림각은 특정 값의 비율의 과다로 인해 그래프로 상관관계를 확인할 수 없어서 회귀분석에서 제외하였다.
절삭력에 대한 상관관계 그래프에서(Figs. 2~3) 절삭 깊이, 절삭 간격, 일축압축강도가 커지면 대체로 절삭력도 증가하는 양상이 나타났다. 수직력에 대한 상관관계 그래프에서(Figs. 4~5)도 절삭 깊이, 절삭 간격, 일축압축강도가 커지면 수직력이 증가하는 양상이 나타났다. 비에너지에 대한 상관관계 그래프에서(Figs. 6~7) 절삭 깊이, 절삭 간격이 증가할 때 비에너지가 감소하였고, 일축압축강도가 증가할 때 비에너지가 증가하였다. 단, 전반적인 경향은 선형회귀 모형을 따랐지만, 데이터의 편차가 있어 결정계수 값은 다소 낮은 값이 기록되었다.
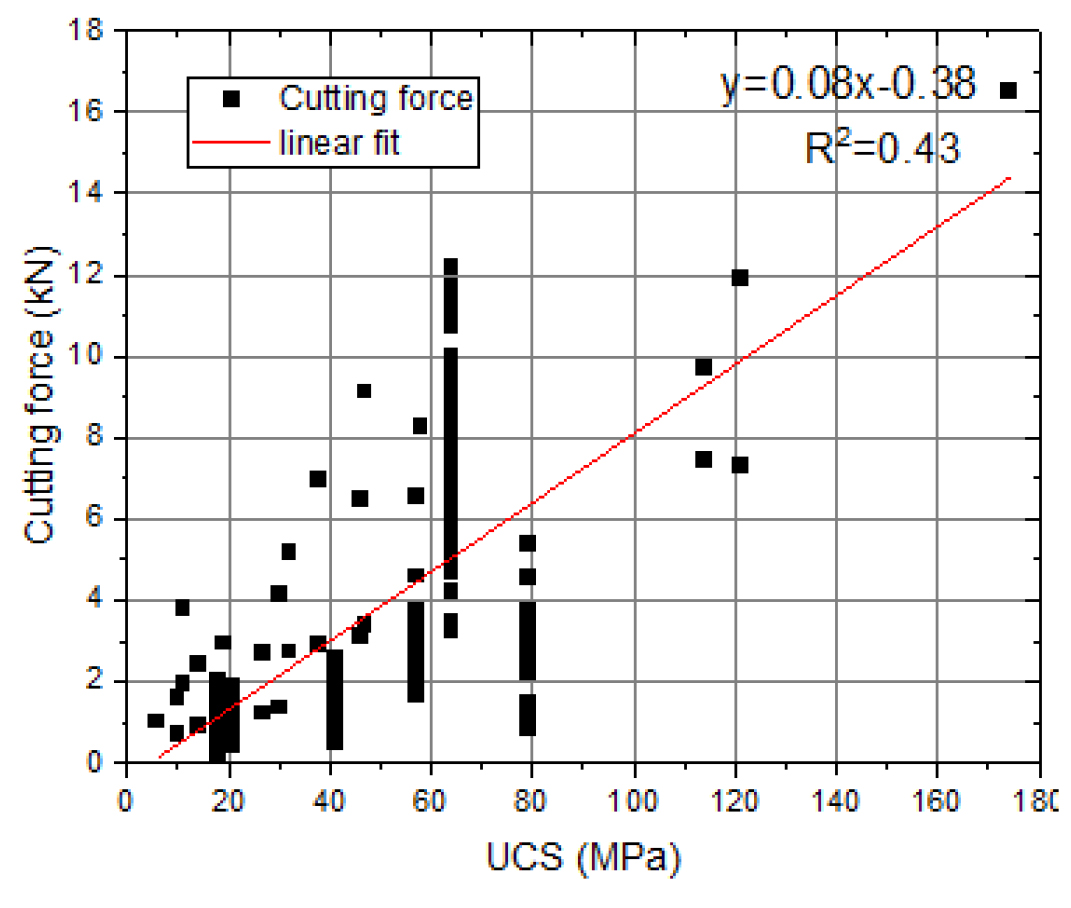
Fig. 2.
Relationship between cutting force and depth, spacing
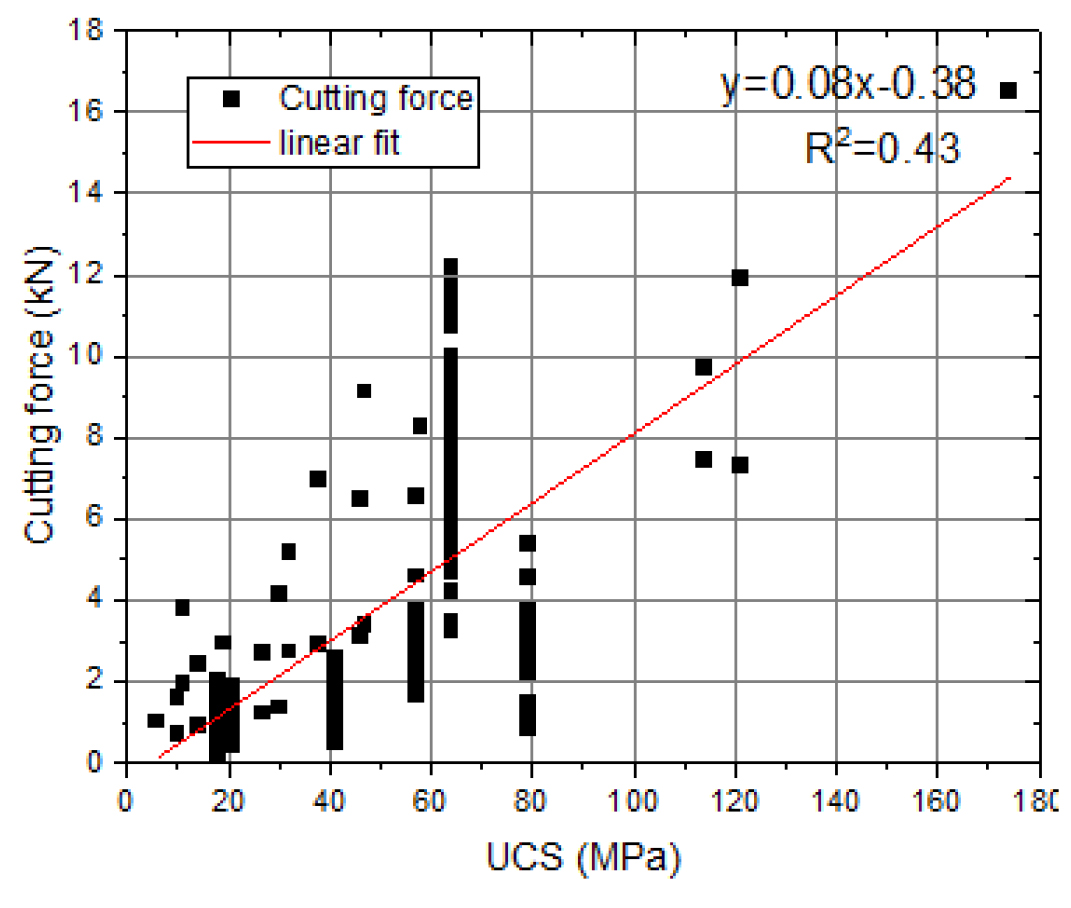
Fig. 3.
Relationship between cutting force and UCS
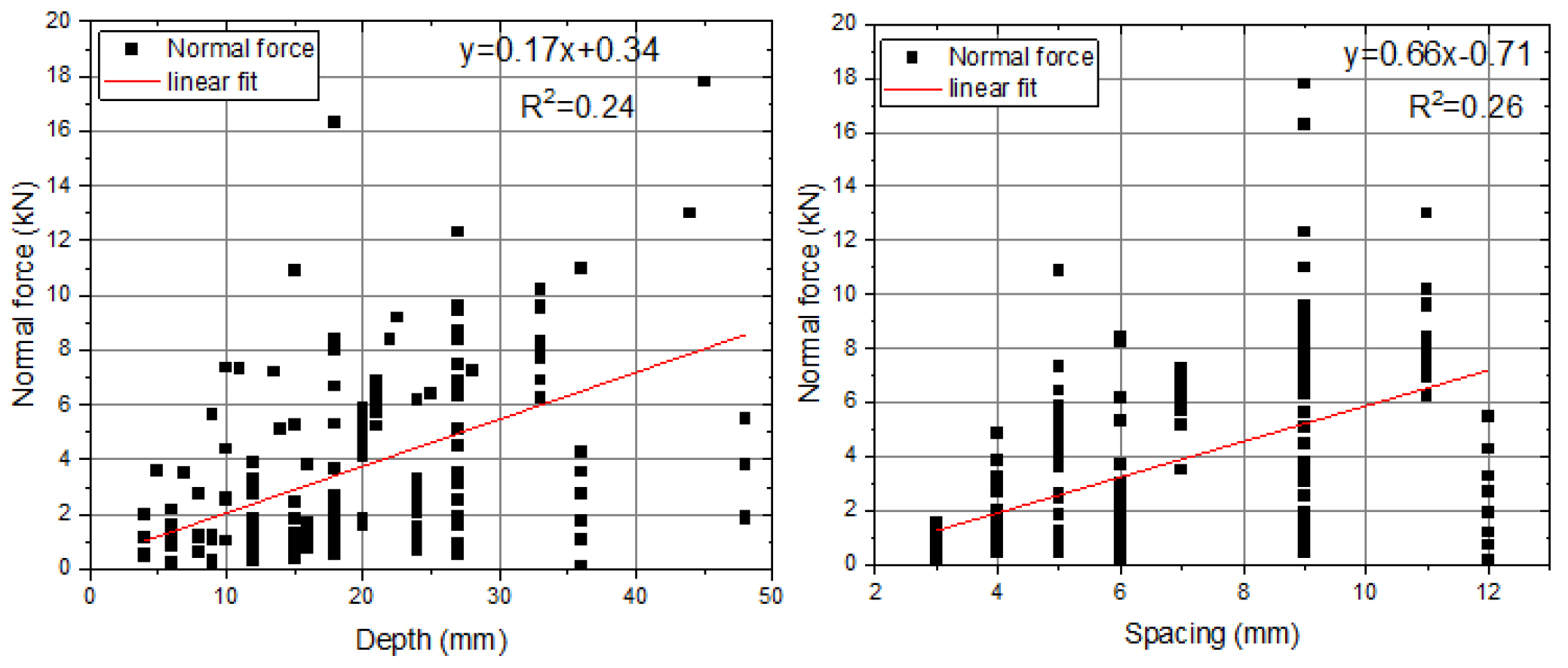
Fig. 4.
Relationship between normal force and depth, spacing
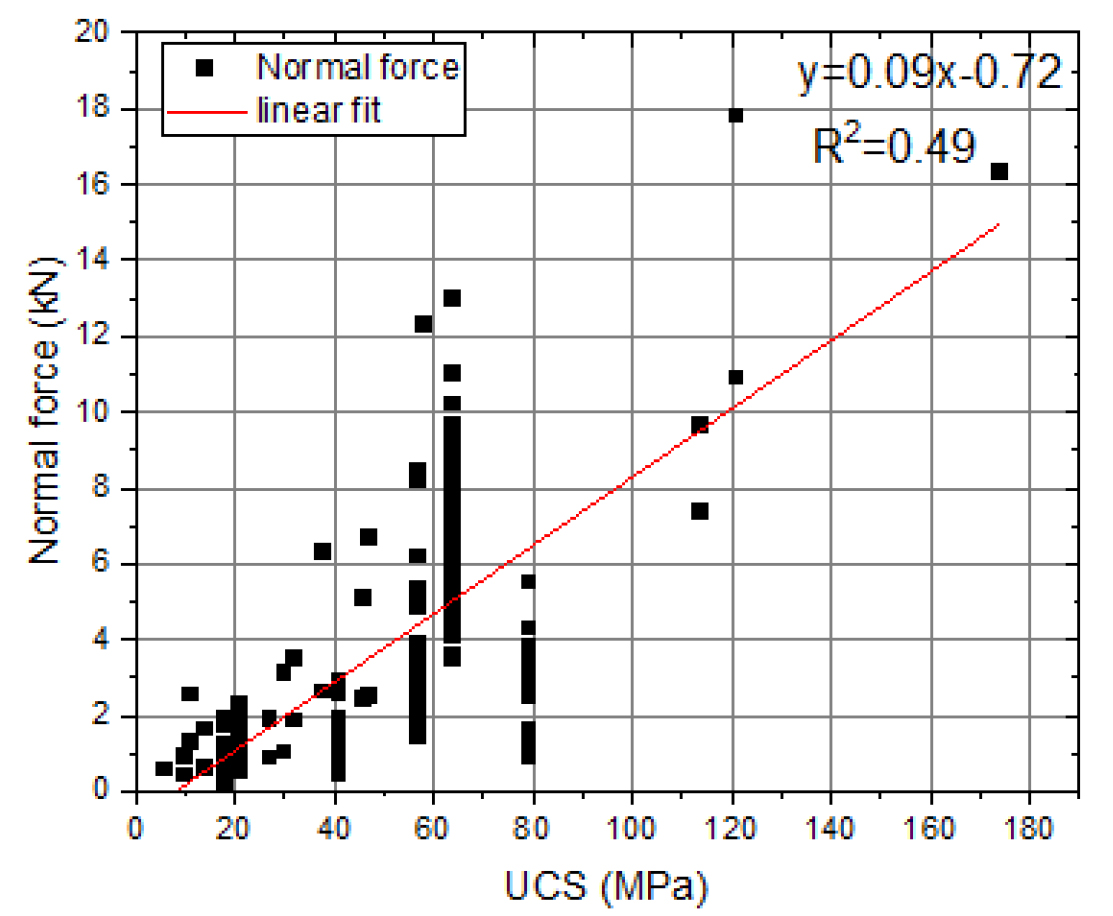
Fig. 5.
Relationship between normal force and UCS
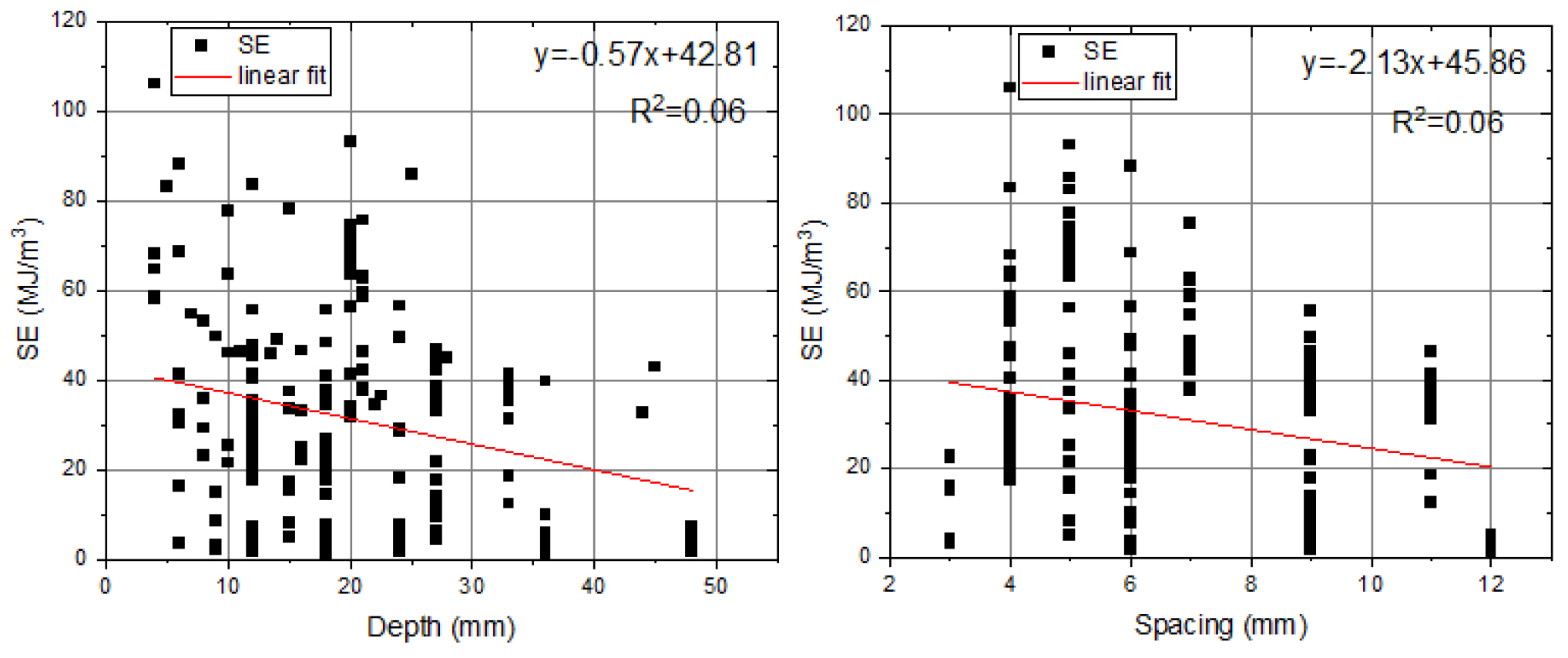
Fig. 6.
Relationship between SE and depth, spacing
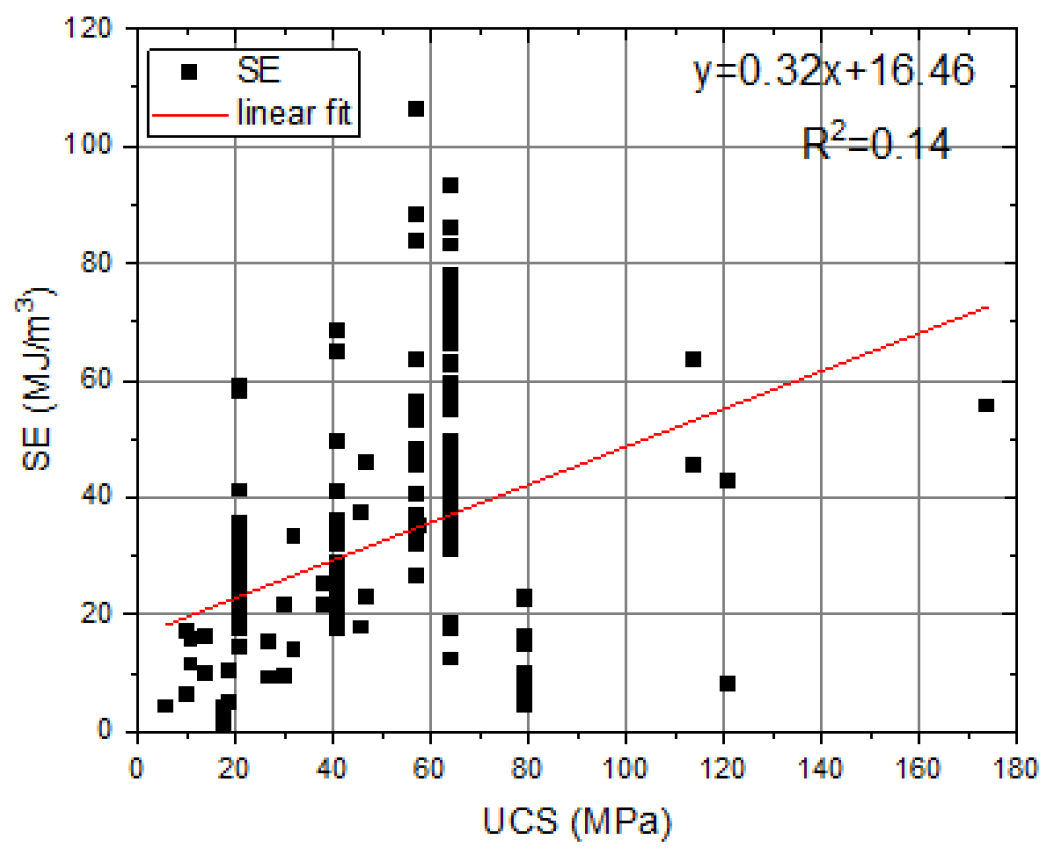
Fig. 7.
Relationship between SE and UCS
3.2 기여도 분석
수집한 데이터들의 분산분석 결과를 Tables 3, 4, 5, 6, 7에 정리하였고, 입력 인자별 기여도를 분석한 결과는 Table 8에 요약하였다. 각 표에서 DF는 자유도, Seq ss는 순차제곱합, Adj MS는 수정평균제곱, F는 검정통계량, P는 유의수준을 나타낸다. 기여도는 전체 순차제곱합 대비 각 입력인자별 순차제곱합이 차지하는 비율로 계산하였다.
먼저 비에너지에 대한 기여도는 절삭 간격 52%, 일축압축강도 21%, 받음각 6%, 절삭 깊이 5%, 비틀림각 2%, 오차 15%다. 평균 절삭력에 대한 기여도는 일축압축강도 29%, 절삭 간격 20%, 받음각 13%, 절삭 깊이 10%, 비틀림각 5%다. 최대 절삭력에 대한 기여도는 일축압축강도 32%, 절삭 간격 17%, 받음각 15%, 절삭 깊이 10%, 비틀림각 6%, 오차 21%다. 평균 수직력에 대한 기여도는 일축압축강도 20%, 절삭 간격 19%, 절삭 깊이 15%, 받음각 14%, 비틀림각 3%, 오차 29%이다. 마지막으로 최대 수직력에 대한 기여도는 절삭간격 29%, 절삭깊이 17%, 일축압축강도 14%, 받음각 3%, 비틀림각 0%, 오차 37%이다.
비에너지에 절삭간격이 가장 지배적인 영향을 미치는 것으로 나타났으며, 일축압축강도는 두 번째의 영향력을 가졌다. 절삭력과 수직력에 가장 큰 영향을 미치는 입력변수는 암석의 일축압축강도, 절삭 간격의 순서였고 영향력이 비슷한 수준이었다. 이는 단일 픽커터의 절삭시험을 기준으로 분석한 결과이기 때문에 암석시편에 따른 최적 절삭 간격이 반영되지 않고, 다양한 절삭 간격이 모두 실험계획에 반영되었기 때문으로 분석된다. 만약 절삭 간격의 입력치가 최적간격에 가깝게 분포하고 있었다면, 일축 압축강도가 절삭력 및 비에너지 모두에 가장 큰 영향인자로 분석되었을 확률이 매우 높다.
출력인자에 대한 입력인자의 유의성 및 기여도의 정확한 분석을 위해서는 실제 실험계획에 따른 실험데이터를 확보해야 하고, 이를 통해 실험계획표상의 통계모델의 해상도를 보다 향상시켜야 한다. 하지만 본 연구에서는 암반 물성과 로드헤더의 운영과 설계에 활용될 데이터 획득에 대한 한계점이 명확히 존재하였다. 이런 이유로 비에너지, 평균 절삭력, 최대 절삭력, 평균 수직력, 최대 수직력에 대한 분산분석의 오차가 15%이상 높게 나온 것으로 판단된다.
본 연구는 실험실 조건에서 수행된 데이터를 기준으로 입출력 인자 간의 기여도를 분석하였다. 따라서 실규모 터널현장의 환경과 로드헤더의 실제 운용조건이 반영되지 않은 한계점이 존재한다. 추후 상이한 역학적 물성을 가지는 암반과 로드헤더 운용조건에 대한 추가적인 실험을 통해 입력변수 변동에 대한 효과를 보다 면밀하게 분석할 예정이다.
Table 3.
ANOVA for specific energy
|
DF
|
Seq SS
|
Adj MS
|
F
|
P
|
UCS
|
2
|
2120
|
1060
|
2.74
|
0.18
|
Depth
|
2
|
482
|
241
|
0.63
|
0.58
|
Spacing
|
5
|
5270
|
1050
|
2.73
|
0.18
|
Attack angle
|
2
|
605
|
303
|
0.78
|
0.52
|
Skew angle
|
2
|
194
|
96.9
|
0.25
|
0.79
|
Error
|
4
|
1540
|
386
| | |
Total
|
17
|
10210
| | | |
S = 19.6385 R-Squared = 84.89% Adjusted R-Squared = 35.78%
|
Table 4.
ANOVA for mean cutting force
|
DF
|
Seq SS
|
Adj MS
|
F
|
P
|
UCS
|
2
|
53.4
|
26.7
|
2.40
|
0.21
|
Depth
|
2
|
19.5
|
9.80
|
0.88
|
0.48
|
Spacing
|
5
|
37.2
|
7.40
|
0.67
|
0.67
|
Attack angle
|
2
|
23.7
|
11.8
|
1.06
|
0.43
|
Skew angle
|
2
|
9.00
|
4.50
|
0.40
|
0.69
|
Error
|
4
|
44.6
|
11.1
| | |
Total
|
17
|
187
| | | |
S = 3.34 R-Squared = 76.22% Adjusted R-Squared = 0.00%
|
Table 5.
ANOVA for peak cutting force
|
DF
|
Seq SS
|
Adj MS
|
F
|
P
|
UCS
|
2
|
477
|
239
|
3.10
|
0.15
|
Depth
|
2
|
145
|
72.3
|
0.94
|
0.46
|
Spacing
|
5
|
249
|
49.9
|
0.65
|
0.68
|
Attack angle
|
2
|
220
|
110
|
1.43
|
0.34
|
Skew angle
|
2
|
94.0
|
47.0
|
0.61
|
0.59
|
Error
|
4
|
308
|
77.0
| | |
Total
|
17
|
1490
| | | |
S = 8.77 R-Squared = 79.39% Adjusted R-Squared = 12.39%
|
Table 6.
ANOVA for mean normal force
|
DF
|
Seq SS
|
Adj MS
|
F
|
P
|
UCS
|
2
|
38.1
|
19.1
|
1.39
|
0.35
|
Depth
|
2
|
28.9
|
14.5
|
1.06
|
0.49
|
Spacing
|
5
|
36.6
|
7.30
|
0.53
|
0.75
|
Attack angle
|
2
|
27.3
|
13.7
|
1.00
|
0.45
|
Skew angle
|
2
|
4.50
|
2.30
|
0.16
|
0.85
|
Error
|
4
|
54.8
|
13.7
| | |
Total
|
17
|
190
| | | |
S = 3.70 R-Squared = 71.20% Adjusted R-Squared = 0.00%
|
Table 7.
ANOVA for peak normal force
|
DF
|
Seq SS
|
Adj MS
|
F
|
P
|
UCS
|
2
|
206
|
103
|
0.76
|
0.53
|
Depth
|
2
|
244
|
122
|
0.90
|
0.48
|
Spacing
|
5
|
416
|
83.2
|
0.61
|
0.70
|
Attack angle
|
2
|
43.0
|
21.6
|
0.16
|
0.86
|
Skew angle
|
2
|
2.00
|
0.90
|
0.01
|
0.99
|
Error
|
4
|
544
|
136
| | |
Total
|
17
|
1460
| | | |
S = 11.66 R-Squared = 62.60% Adjusted R-Squared = 0.00%
|
Table 8.
Analysis of contribution rates
|
SE
(MJ/m3)
|
Mean cutting force
(kN)
|
Peak cutting force
(kN)
|
Mean normal force
(kN)
|
Peak normal force
(kN)
|
UCS
|
21%
|
29%
|
32%
|
20%
|
14%
|
Depth
|
5%
|
10%
|
10%
|
15%
|
17%
|
Spacing
|
52%
|
20%
|
17%
|
19%
|
29%
|
Attack angle
|
6%
|
13%
|
15%
|
14%
|
3%
|
Skew angle
|
2%
|
5%
|
6%
|
3%
|
0%
|
Error
|
15%
|
24%
|
21%
|
29%
|
37%
|
Total
|
100%
|
100%
|
100%
|
100%
|
100%
|
4. 결 론
실제 굴착 현장에서 측정 장비를 붙여 데이터를 취득하는 연구는 현장여건상 수행하기가 매우 어렵다. 따라서 본 보고는 입력인자가 출력인자에 미치는 영향을 분석하기 위하여 기존 문헌의 데이터를 수집하여 분석하였다. 선행 연구에서 추출한 절삭시험 데이터를 입력값과 출력값으로 구분하여 다구찌 실험계획법으로 작성된 직교배열표에 기입하였다. 그 후 분산분석을 실시하여 출력 인자에 대한 입력 인자의 기여도를 분석했다. 이를 통해 얻어진 결과를 요약하면 아래와 같다.
비에너지에 미치는 영향은 절삭 간격의 기여도가 가장 컸고, 절삭력에는 일축압축강도의 기여도가 가장 컸다. 평균 수직력은 일축압축강도의 기여도가 가장 컸으며, 최대 수직력은 절삭 간격의 기여도가 가장 높았다.
결과적으로 암반강도뿐만 아니라 커터간격과 같은 커팅헤드 설계인자도 로드헤더의 굴진 성능에 많은 영향을 미치는 것으로 분석되었다. 따라서 일축압축강도와 함께 로드헤더의 커팅헤드의 설계 인자도 함께 고려하여 굴진 예측 모델을 구성하면 보다 정확한 거동예측이 가능할 것으로 판단된다.
기여도 분석 결과에 따르면 오차의 비율이 비교적 높게 나왔다. 직교배열표에 선행 연구 결과를 기입하는 과정에서 직교배열표와 일치하지 않는 데이터는 평균값을 사용하여 분석 정확도가 낮아진 것으로 판단된다. 이는 본 기술보고의 한계점으로서 추가적인 실험을 통해 입력변수 변동에 대한 효과를 보다 면밀하게 분석할 예정이다.
Acknowledgements
본 연구는 2022년도 국토교통부(국토교통과학기술진흥원) 국토교통기술촉진연구사업의 ‘파일럿시험 및 현장데이터 기반 로드헤더 굴진율 수정 예측모델 개발(22CTAP-C164190-02)’ 과제를 통해 수행되었습니다.
References
Bilgin, N., Yazici, S., and Eskikaya, S., 1996, A Model to Predict the Performance of Roadheaders And Impact Hammers In Tunnel Drivages, Presented ate the ISRM Symposium, Italy.
Bilgin, N., Tumac, D., Feridunoglu, C., Karakas, A.R., and Akgul, M., 2005, The performance of a roadheader in high strength rock formations in Küçüksu tunnel, Proceedings of the International World Tunnel Congress and the 31st ITA General Assembly, Istanbul, Turkey, 7-12 May 2005, pp.815-820
Bilgin, N., Demircin, M.A., Copur, H., Balci, C., Tuncdemir, H., and Akcin, N., 2006, Dominant rock properties affecting the performance of conical picks and the comparison of some experimental and theoretical results. International Journal of Rock Mechanics & Mining Sciences, 43, 139-156.
10.1016/j.ijrmms.2005.04.009Jeong, H., Choi, S., Lee, S., and Jeong, S., 2020, Rock Cutting Simulation of Point Attack Picks Using the Smooth Particle Hydrodynamics Technique and the Cumulative Damage Model, Applied Sciences, 10(15).
10.3390/app10155314Park, J., Kang, H., Lee, J., Kim, J., Oh, J., Cho, J., Rostami, J., and Kim, H., 2018, A study on rock cutting efficiency and structural stability of a point attack pick cutter by lab-scale linear cutting machine testing and finite element analysis, nternational Journal of Rock Mechanics and Mining Sciences, 103, 215-229.
10.1016/j.ijrmms.2018.01.034Rostami, J., Ozdemir, L., and Neil, D.M., 1994, Performance prediction: A key issue in mechanical hard rock mining. Mining Engineering, 11, 1263-1267.
Rostami, J., 2011, Section 7.1 Rock Breakage, Mechanical, Mining Engineering Handbook, Society of Mining, Metallurgy, and Exploration Engineering Inc (SME).
Restner, U. and Plinninger, R., 2015, Rock Mechanical Aspects of Roadheader Excavation. EUROCK 2015 & 64th Geomechanics ColloquiumAt: Salzburg, Austria, October 2015.
Taguchi, G., and Phadke, M.S., 1989, Quality Engineering through Design Optimization. Quality Control, Robust Design, and the Taguchi Method, 77-96.
10.1007/978-1-4684-1472-1_5Thuro, K. and Plinninger, R.J., 1998, Geological limits in roadheader excavation-Four case studies, Proceedings of the 8th International IAEG Congress, pp.3545-3552.
Thuro, K. and Plinninger, R.J., 1999, Roadheader excavation performance-geological and geotechnical influences, Proceedings of the 9th ISRM Congress, Paris, pp.1241-1244.
Wang, X., Su, O., Wang, Q., and Liang, Y., 2017, Effect of cutting depth and line spacing on the cuttability behavior of sandstones by conical picks, Arabian Journal of Geosciences, 10, 525.
10.1007/s12517-017-3307-3