1. 서 론
2. 실험 개요
2.1 시험편 제작
2.2 실험 장치 및 방법
3. 실험 결과
3.1 역학적 조건
3.2 수리-역학적 조건
4. 고 찰
4.1 거칠기가 마찰회복률에 미치는 영향
4.2 수리-역학적 조건이 마찰회복률에 미치는 영향
5. 결 론
1. 서 론
고준위방사성폐기물은 인간 생활권으로부터 영구적으로 안전하게 격리되어야 하며, 이를 위해 현재까지 다양한 처분 개념들이 제시되었다. 이 중 다중 방벽(multi-barrier system) 개념을 적용한 심층처분(deep geological disposal, DGD)이 안정성뿐 아니라 경제성 측면에서도 효율적인 것으로 알려져 있다(IAEA, 2011). 다중 방벽은 처분용기, 완충재, 뒤채움재 등으로 방사성 핵종의 유출을 일차적으로 막아주는 공학적 방벽(engineered barrier system, EBS)과 이를 둘러싼 암반과 토양 등을 의미하는 천연방벽(natural barrier system, NBS)으로 구성되어 있으며, 여기서 천연방벽은 처분시설을 물리적으로 지지함과 동시에 방사성 핵종의 이동을 지연시키는 역할을 최소 수십만년 이상의 장기간 동안 수행해야 한다. 따라서 지질학적 장기진화를 고려한 천연방벽 성능평가 연구가 필수적이며, 처분 선도국들은 천연방벽 암반의 지구조적 장기진화를 수리-역학적 연계 모델을 통해 평가하고 있다(Valli et al., 2011, Hakala et al., 2019). 천연방벽의 수리-역학적 장기진화 평가에 있어 가장 중대한 영향을 미치는 것은 단층(faults), 절리(joints) 등과 같은 암반 불연속면(rock discontinuities)의 존재이다. 암반은 일반적으로 투수계수가 낮은 특성이 있으나, 높은 취성으로 인해 필연적으로 불연속면이 생성되어 전파되기 때문이다. 불연속면 중에서는 암반 절리의 빈도가 가장 높다고 할 수 있으며, 이러한 절리는 유체의 잠재적 유동 경로가 되어 천연방벽의 수리-역학적 특성을 결정짓는 주요 요소로 작용하게 된다. 따라서 천연방벽의 장기진화 검토 시 암반 내 절리의 장기거동 특성을 파악하는 것은 필수적이라 할 수 있다.
암반 절리의 장기거동 특성은 절리의 변형이 발생하기 전과 후로 나누어 살펴볼 수 있으며, 변형이 발생한 이후에는 절리면 내 거칠기 간 접촉면적과 응력이 가해지는 시간이 거동에 영향을 미치게 된다. 일반적으로 변형 발생 후에는 절리면 전체가 아닌 실제 접촉된 면적에 응력이 집중되며, 시간 경과에 따라 응력 이완 현상이 발생하게 된다. 이후 지각 작용 등으로 인해 절리면을 따라 다시 미끄러짐이 발생하였을 때 거칠기의 영향이 증가함으로 인해 마찰계수가 증가하는 현상이 나타나게 되는데, 이를 가리켜 마찰회복(frictional healing) 현상이라고 한다. 재변형 발생 시 마찰계수의 증가량이 클수록 절리면에 응력이 축적될 수 있는 양이 커짐을 의미하며, 이는 절리 장기거동과 직접적 관계를 갖기 때문에 지진 또는 암반 절리의 장기거동에 따른 천연방벽의 안정성을 평가하기 위한 연구가 다양한 분야에서 진행되고 있다.
암반 절리의 마찰회복 거동을 파악하기 위한 실험적 연구들에서는 슬라이드-홀드-슬라이드(slide-hold-slide, SHS) 실험이 대표적으로 활용되고 있다. SHS 실험은 절리의 미끄러짐 및 멈춤 과정 반복에 따른 전단응력의 이완, 축적과 마찰계수의 변화를 정량적으로 평가하기 위한 실험으로(Marone, 1998, Tesei et al., 2012, Woo et al., 2016), Fig. 1과 같이 절리 거동이 안정적 미끄러짐(steady state) 단계에 도달한 후, 일정한 속도의 전단변형 발생(Fig. 1의 ①), 일정 시간 동안 전단변형 멈춤(Fig. 1의 ②), 전단변형의 재발생(Fig. 1의 ③)을 순서대로 수행하게 된다.
실험 결과 분석 시에는 멈춤 이전 안정한 미끄러짐 상태의 운동마찰계수(μd)와 다시 미끄러짐을 발생시켰을 때 측정되는 최대정지마찰계수(μs)를 측정하게 되며, 전단변형을 멈추는 멈춤 시간(holding time)이 길어질수록 두 마찰계수 간의 차이인 마찰회복량 Δμ가 증가하는 경향을 보이게 된다(Marone, 1998, Yasuhara et al., 2005, Kishida et al., 2011, 2012, 2014). 이때 시간에 따른 마찰회복량은 멈춤 시간(th)의 로그값과 선형적 관계를 나타내는 것으로 알려져 있으며, 식 (1)에서와 같이 마찰회복계수(β)라고 정의하고 있다. 식 (1)에서 멈춤 시간의 단위는 sec가 적용된다.
또한 Dieterich(1972, 1974)는 다수의 실험을 통해 미끄러짐 재발생 시 마찰회복은 절리 표면의 소성, 점소성 거동 및 절리 경계면 내 가루(powder) 형태 부산물인 암석 비지(gouge) 증가로 인해 접촉면적이 증가함에 따라 절리에 작용하는 전단응력이 변화하기 때문에 발생하는 것으로 보고한 바 있으며, 식 (2)와 같이 전단응력 및 시간 경과에 따른 마찰회복을 표현하였다. 여기서 A값은 마찰회복률로써 매질 및 실험조건에 따라 변화하는 물질상수로 정의한 바 있다. 식 (2)에서 전단응력 및 멈춤 시간의 단위는 각각 MPa, sec가 적용된다.
그 밖에 Kishida et al.(2011)은 마찰회복계수가 물질에 따라 달라지는 변수로써 절리면에 작용하는 수직응력 및 절리면 압축강도와 관련되어 있다고 밝힌 바 있으며, Kishida et al.(2012)은 직접전단시험을 통해 암종별, 절리 표면의 습윤 상태 여부에 따라 마찰회복계수 변화를 살펴본 바 있다. 실험결과를 통해 마찰회복계수 특성이 암종에 따라 다르게 나타나며 불연속면 표면이 습윤 상태일 경우 마찰회복계수가 증가하는 경향이 나타남을 보고한 바 있다.
본 연구에서는 천연방벽의 수리-역학적 장기진화와 관련하여 거칠기 및 습윤 상태 여부에 따른 암반 절리의 마찰회복 거동을 분석하고자 하였다. 이를 위해 시멘트 모르타르로 제작된 절리 시험편을 표면이 건조(dry) 상태인 역학적 조건과 젖은(wet) 상태인 수리-역학적 조건으로 나누어 SHS 실험을 수행하였다. 그리고 실험 결과로부터 Dieterich(1972)가 정의한 마찰회복률 A값을 도출하여 비교함으로써 수리-역학적 조건이 암반 절리의 마찰회복 거동에 미치는 영향에 대해 분석하였다.
2. 실험 개요
2.1 시험편 제작
암석 절리 시험편은 동일한 물성 및 거칠기를 지니는 시료의 재현이 불가능하여 다양한 조건 하에서의 거동 분석에 어려움이 있기 때문에 본 연구에서의 SHS 실험에서는 시멘트 모르타르로 제작된 유사암석 절리 시험편을 이용하였다. 유사암석 절리 시험편 제작에 사용된 시멘트 재료는 ㈜유니온의 그라우트 HS이며, 물과 재료의 중량비를 15 : 100으로 혼합하여 제작하였다. 이렇게 제작된 시험편은 10일의 수중 양생 후 80 MPa 이상의 단축압축강도가 발현되는 것으로 알려져 있으며(Kim and Jeon, 2016), 암석과 유사한 전단거동 특성을 보이는 절리 시험편 제작이 가능하다고 보고된 바 있다(Park et al., 2013, Lee et al., 2014).
시험편에 대한 기본 물성은 10회 이상의 실험 결과로부터 도출하였으며, 그 평균값을 정리하면 Table 1과 같다. 여기서 절리면 압축강도(joint wall compressive strength, JCS)와 기본 마찰각(basic friction angle)은 거칠기가 없는 매끈한 표면에서 각각 슈미트 해머 반발경도 시험(Schmidt hammer rebound hardness test)과 경사각 시험(tilt test)을 수행하여 도출하였다.
Table 1.
Physical and mechanical properties of cement mortar specimens
절리 시험편 제작은 선행연구(Kim and Jeon, 2019)에서 활용했었던 제작툴을 이용하였다. Fig. 2(a)와 같은 알루미늄 몰딩틀을 통해 하부 시험편을 제작하고, 이를 Fig. 2(b)와 같이 거치시켜 상부 시험편을 제작하였다. 서로 다른 거칠기를 지니는 알루미늄 몰딩틀을 제작하여 2 종류의 거칠기를 지니는 시험편들을 제작하였으며, 제작된 시험편을 대상으로 Fig. 3과 같이 3차원 레이저 스캐닝을 수행하여 거칠기를 분석한 결과 JRC(joint roughness coefficient)가 각각 2.05, 11.63으로 나타났다. JRC는 전단방향과 수평한 방향에 대해 0.5 mm의 간격으로 1차미분의 평균제곱자승근(Z2)을 측정하고 (식 (3)), 그 평균값을 Tse and Cruden(1979)이 제안한 식 (4)의 상관관계식에 대입하여 도출한 결과이다. 식 (3)에서 x, y는 각 측정점의 좌표이며, L은 개별 프로파일의 길이를 의미한다. 따라서 x, y, L은 모두 동일한 단위가 적용되어야 한다.
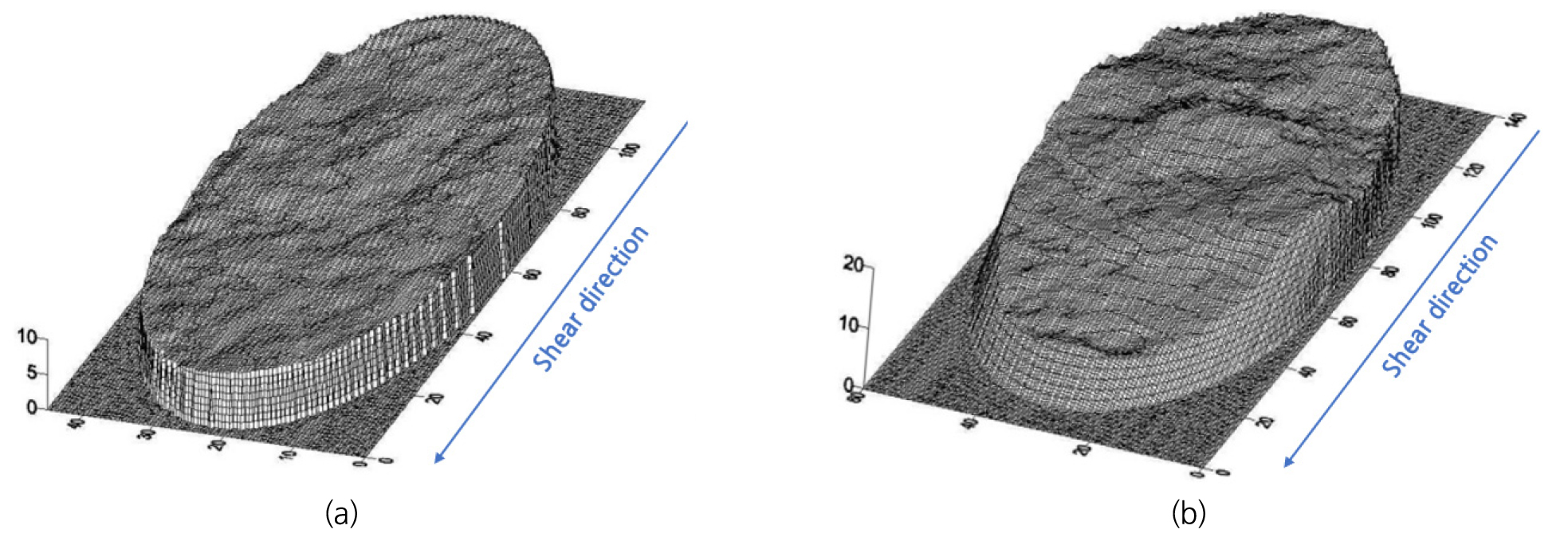
Fig. 3
Three-dimensional profiles of cement mortar specimens: (a) JRC = 2.05; (b) JRC = 11.63 (modified from Kim and Jeon, 2016)
2.2 실험 장치 및 방법
일반적으로 암반 절리의 마찰회복 거동은 전단조건 하에서 분석이 이루어지기 때문에 SHS 실험은 직접전단 조건에서 수행하게 된다. 하지만, 직접전단실험은 절리가 공기 중에 노출되어 있기 때문에 수압을 정밀하게 조절해야 하는 수리-역학적 조건을 구현하는데 한계가 있다. 따라서 본 연구에서는 절리면에 일정압력의 물을 주입하는 수리-역학적 조건에서의 실험을 위해 삼축압축 조건 하 전단실험을 수행하였다. 이 실험법은 시험편이 밀폐된 삼축 챔버 내에 위치하기 때문에 절리면에 작용하는 수압을 정밀하게 조절하는데 용이하기 때문이다.
삼축압축 조건 하 전단실험에는 실내암석시험용으로 널리 활용되고 있는 MTS 816 시스템을 이용하였다. 이 장치는 Fig. 4와 같이 MTS 316 하중 프레임(main frame), 삼축 챔버(triaxial chamber), 구속압 유닛(confining pressure unit), 공극압 증압기 (pore-pressure intensifier) 및 자료수집(DAQ) 시스템을 포함한 기타 악세서리류(additional accessories)로 구성되어 있으며, 공극압 증압기를 통해 물을 주입하는 것이 가능하다.
본 연구에서는 절리면에 직접 물을 주입하기 위해 Fig. 5(a)와 같이 시험편에 물 주입공(water injection hole)을 천공하였으며, 이후 Fig. 5(b)와 같이 삼축 챔버 내에 시험편을 위치시켜 실험을 수행하였다. Fig. 5(c)는 실험이 준비된 상태의 모식도를 보여주고 있으며, 여기서 축하중 방향과 절리가 이루는 각도는 28°가 되도록 시험편을 준비하였다. 이 각도는 선행연구(Kim and Jeon, 2011)를 통해 도출된 삼축압축 조건 하에서 무결암 시험편에 나타나는 일반적인 파괴면 각도이다. 그리고 모식도 내에서 확인할 수 있듯이 축방향 변위는 장치 내 설치된 LVDT, 횡방향 변위는 신율계(extensometer)를 이용하여 각각 측정하였다. 이와 같은 실험 시스템은 열-수리-역학적 조건 하에서 암반 절리의 전단거동 분석에 활용되어 적용성이 검증된 바 있다(Kim and Jeon, 2019).
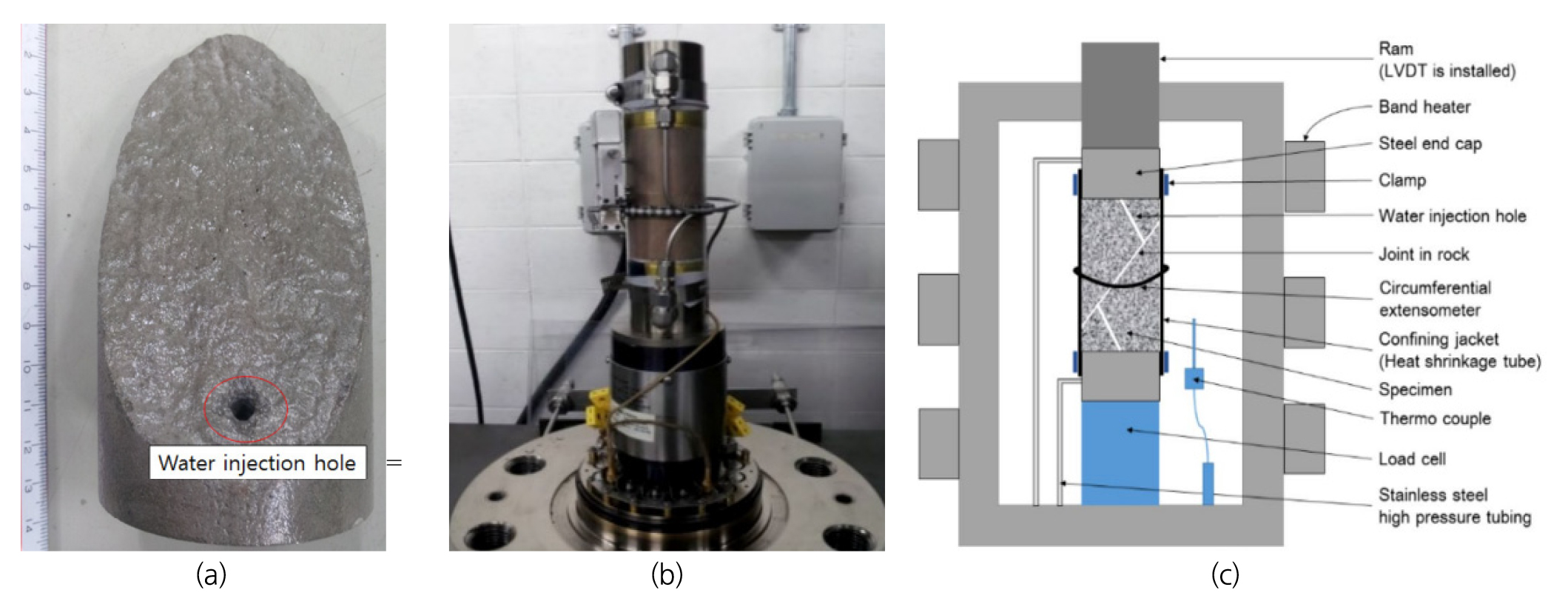
Fig. 5
Experimental setup used in this study: (a) a cement mortar specimen with a water injection hole; (b) a specimen assembly inside of the triaxial chamber; (c) a schematic diagram of the experimental system (Kim and Jeon, 2019)
SHS 실험은 물 주입 여부에 따라 절리 시험편의 표면이 건조된 상태인 역학적 조건(Mechanical conditions, M)과 젖은 상태인 수리-역학적 조건(Hydro-mechanical conditions, HM)으로 나누어 수행하였다. 두 조건에서 JRC가 서로 다른 시험편들을 대상으로 실험을 수행하였으며, 축하중 조건으로는 국제암반공학회(International Society for Rock Mechanics and Rock Engineering, ISRM)의 표준시험법 조건을 만족하는 0.4 mm/min의 변위제어 방식을 적용하였다(Kovári et al., 1983). 그리고 멈춤 시간(holding time)은 두 조건에서 동일하게 60-900 초 사이에서 3개 이상을 선정하여 적용하였다. Table 2는 여기에 구속압 및 수압을 포함한 상세한 실험 조건을 보여주고 있다. 구속압은 역학적 조건에서 0.5-20.0 MPa을 적용하였으며, 수리-역학적 조건에서는 3 MPa의 수압을 고려하여 3.5-20.0 MPa을 적용하였다. 단, 역학적 조건에서 20 MPa의 구속압과 수리-역학적 조건에서 10 MPa 이상의 구속압은 추가적인 경향성 분석을 위해 특정 거칠기에만 적용하였으며, 이는 Table 2에 괄호 및 바닥글로 표기하였다.
Table 2.
Experimental conditions for the SHS tests conducted in this study
3. 실험 결과
암반 절리의 마찰회복 거동은 SHS 실험 결과에서 멈춤 시간에 따른 전단강도의 변화량을 의미하는 마찰저항 회복(frictional resistance recovery)을 통해 분석할 수 있다. 이는 전단강도 회복(shear strength recovery) 또는 전단응력 회복(shear stress recovery)으로 표현하기도 하며 Δr로 표기하는 것이 일반적이다. 따라서 마찰저항 회복을 분석하기 위해서는 전단변위-전단응력 관계의 도출이 요구된다. 본 연구에서 수행한 삼축압축 조건 하 전단실험은 절리면에서의 전단변위와 전단응력이 직접적으로 측정되지 않기 때문에 추가적인 계산이 요구된다. 이는 절리면에 작용하는 수직응력 또한 마찬가지이다. 본 연구에서는 측정된 축방향 및 횡방향 변위로부터 전단변위를 계산하였으며, 절리면에 작용하는 전단 및 수직응력은 식 (5), (6)의 관계식을 이용하여 계산하였다.
위 식에서 σa는 축방향 응력(axial stress), Pc는 구속압(confining pressure), θ는 축하중 방향과 절리가 이루는 각도를 의미한다. 따라서 모든 시험편들에서 θ는 28°로 동일한 값이 적용된다. 그리고 유효 구속압(effective confining pressure)은 역학적 조건에서는 구속압과 동일하고, 수리-역학적 조건에서는 구속압과 수압(3 MPa)의 차이가 된다.
Fig. 6은 삼축압축 하 SHS 실험에서 위와 같은 계산을 통해 도출한 결과의 예시를 보여주고 있다. 좌측 그림과 같은 전단변위-전단응력 관계가 도출되며, 여기서 마찰회복 거동은 우측 그림과 같이 나타난다. 멈춤 시간이 증가함에 따라 점차 전단응력이 높은 수준으로 회복되는 전형적인 SHS 실험 결과를 나타내고 있는 것을 확인할 수 있다. 이러한 결과를 이용하여 Fig. 7과 같이 각 멈춤 시간에 따른 마찰저항 회복을 식 (2)의 관계식으로 회귀함으로써 마찰회복률 A값을 분석하였다.
3.1 역학적 조건
역학적 조건은 절리 시험편의 표면에 물을 주입하지 않고 건조된 상태에서 실험을 수행하였다. 삼축압축 하 전단실험에서는 구속압이 일정하게 유지되기 때문에 축방향 응력이 변화하면서 절리면에 작용하는 수직응력 계산값이 조금씩 차이를 보이게 된다. 하지만, 전단변위를 구속하는 홀드 단계부터는 작용 수직응력이 거의 일정하게 유지되는 경향을 보였다. 따라서 처음 홀드가 시작되는 시점에서 식 (5)로 계산되는 작용 수직응력을 해당 실험에서의 유효 수직응력(effective normal stress)로 정의하였다.
서로 다른 거칠기를 지닌 시험편들에 대해 수행한 역학적 조건 하 SHS 실험 결과를 요약하면 Table 3과 같으며, 여기서 시험편들은 JRC가 2.05, 11.63인 경우에 대해 각각 M-L, M-H를 붙여 표기하였다. 마찰회복률 A값의 분석을 위해 멈춤 시간에 따른 마찰저항 회복을 분석한 결과는 Fig. 8과 같으며, 멈춤 시간에 비례하여 마찰저항 회복이 점차 증가하는 경향성을 확인할 수 있다. 이는 멈춤 시간이 증가함에 따라 절리면에서 발생하는 크립 변형(creep deformation)이 더 크게 발생하고, 이것이 절리면의 접촉면적(contact area) 증가에 까지 영향을 미치기 때문이다(Dieterich and Kilgore, 1994). A값은 이 결과로부터 회귀분석을 수행하여 도출하였으며, 회귀선은 Fig. 8 내에서 점선으로 나타내었다.
JRC가 2.05인 시험편들에 대해서는 1.0, 2.0 MPa의 구속압 조건에서의 실험을 2회씩 수행하였는데, 이는 전단파괴로 인한 거칠기 손상의 차이 또는 실험 편차로 인해 동일한 구속압 조건일지라도 유효 수직응력이 다르게 계산될 수 있기 때문이다. 실제로 유효 수직응력과 A값이 약간의 차이를 보이고 있음을 분석 결과에서 확인할 수 있다.
Table 3.
Experimental conditions and analysis results under mechanical conditions
역학적 조건 하에서 유효 수직응력에 따른 마찰회복률 A값의 변화를 살펴보면, 두 거칠기 시험편들에서 모두 유효 수직응력이 증가함에 따라 A값이 증가하는 경향성을 보이는 것을 확인할 수 있다. 이러한 유효 수직응력과 A값의 비례관계에 대해서는 Kishida et al.(2011)에 의해서 보고된 결과와 일치하며, 그 원인에 대해서는 논의된 바 없다. 본 연구에서는 이러한 경향이 높은 유효 수직응력으로 인해 증가된 절리면 접촉면적이 영향을 미쳤기 때문으로 판단하고 있으며, 이로부터 절리면 접촉면적과 마찰회복률이 서로 비례관계에 있을 것이라는 잠정적 결론을 얻을 수 있었다. 다만, 절리면의 접촉면적을 정량적으로 분석하지는 않았기에 추후 다수의 시험편들을 이용하여 이에 대한 추가 분석이 필요할 것으로 판단된다.
3.2 수리-역학적 조건
수리-역학적 조건은 절리면에 일정압력의 물을 주입하여 표면이 젖은 상태에서 실험을 수행하였다. 시험편 내에 물 주입공을 통해 절리면에 직접적으로 물을 주입하였으며, MTS 816 시스템에 포함된 공극압 증압기를 이용하여 실험이 진행되는 동안 3 MPa의 수압이 유지되도록 하였다.
결과 분석은 역학적 조건에서와 마찬가지 방법으로 유효 수직응력과 마찰회복률 A값을 도출하여 수행하였고, 분석 결과는 Table 4에 요약하였다. 그리고 Fig. 9는 마찰회복률 A값의 도출을 위해 수행한 회귀 분석 결과를 보여주고 있다. 수리-역학적 조건에서는 JRC가 2.05, 11.63인 경우에 대해 각각 HM-L, HM-H를 붙여 표기를 하였고, 역학적 조건에서와 동일한 이유로 일부 조건들에 대해서는 반복 실험을 수행하였다. Fig. 9의 결과를 살펴보면 두 거칠기 시험편들에서 모두 멈춤 시간과 마찰저항 회복 간 비례관계가 잘 나타났으며, 이로부터 수리-역학적 조건 하에서도 멈춤 시간이 증가함에 따라 절리면의 접촉면적이 증가한다는 것을 확인할 수 있었다.
또한, 수리-역학적 조건 하에서도 역학적 조건에서와 마찬가지로 두 거칠기 시험편들에서 모두 유효 수직응력과 A값이 비례하는 결과를 보였다. JRC가 2.05인 시험편들(HM-L)에 대해서는 10 MPa 이상의 유효 수직응력 하에서 실험이 수행되지 못하여 상대적으로 낮은 유효 수직응력에서의 결과들만이 제시되어 있는데, 여기서도 분명한 경향성을 확인할 수 있기에 높은 수직응력 하에서도 유사한 경향을 나타낼 것으로 예측되었다. 따라서 절리면의 표면이 젖은 상태인 수리-역학적 조건일지라도 유효 수직응력이 증가하면 절리면의 접촉면적과 마찰회복률이 이에 따라 증가하는 거동 특성에는 변함이 없음을 확인할 수 있었다.
Table 4.
Experimental conditions and analysis results under hydro-mechanical conditions
4. 고 찰
실험 결과들을 종합해보면, 모두 멈춤 시간에 따라 마찰저항 회복이 증가하는 전형적인 SHS 실험 결과가 잘 도출되고 있음을 확인할 수 있다. 그리고 유효 수직응력과 마찰회복률 A값이 비례하는 경향은 서로 다른 실험 조건일지라도 동일하게 나타났다. 하지만, 각 실험 조건에 따라 A값의 크기는 서로 차이를 보였으며, 이는 실험 조건이 마찰회복률에 영향을 미치고 있음을 의미한다. 따라서 이 장에서는 실험 조건이 암반 절리의 마찰회복률에 미치는 영향에 대해 논의하였다.
4.1 거칠기가 마찰회복률에 미치는 영향
거칠기가 서로 다른 암반 절리에서도 대부분의 경향성은 동일하게 나타나는 것을 실험 결과로부터 확인하였다. 하지만, 유효 수직응력에 따른 마찰회복률 A값의 결과를 살펴보면, 거칠기가 더 큰 시험편들이 전반적으로 높은 마찰회복률을 나타내었다. Fig. 10은 서로 다른 두 거칠기의 시험편에 대한 유효 수직응력에 따른 A값의 변화를 비교하여 보여주고 있으며, 역학적 조건 및 수리-역학적 조건에서 모두 JRC가 11.63인 시험편들이 전반적으로 높은 마찰회복률을 나타내고 있음을 확인할 수 있다.
실험별로 유효 수직응력이 차이를 보였기 때문에 동일한 응력 수준에서의 정량적인 비교분석은 수행되지 못하였다. 하지만, 대부분의 응력 수준에서 거칠기가 큰 시험편의 마찰회복률이 크게 나타났기에, 암반 절리의 거칠기가 클수록 마찰회복률은 증가한다는 결론을 얻을 수 있었다. 거칠기가 클수록 전단강도 이후 거칠기 손상(joint surface degradation)이 크게 나타나는데(He et al., 2020), 이로 인해 절리면 내 접촉면적의 변화도 상대적으로 커지기 때문에 거칠기와 마찰회복률이 서로 비례하는 결과를 보인 것으로 판단된다.
4.2 수리-역학적 조건이 마찰회복률에 미치는 영향
역학적 조건 및 수리-역학적 조건 하에서 대부분의 경향성은 동일하게 나타났으나, 수리-역학적 조건에서의 실험 결과들에서 전반적으로 높은 마찰회복률 A값을 나타내었다. 이는 각 실험 조건에서 유효 수직응력에 따른 A값의 변화에 대한 비교결과를 나타낸 Fig. 11에서 확인할 수 있다. 절리면 표면이 젖은 상태인 수리-역학적 조건에서는 멈춤 시간이 길어짐에 따라 광물 용해와 같은 화학 작용이 활성화되어 접촉면적이 추가적으로 증가할 수 있으며(Kishida et al., 2011), 이것이 역학적 조건에 비해 더 높은 마찰회복률을 나타낸 원인으로 판단된다. 또한, 거칠기가 더 큰 시험편들에서 더 분명한 차이를 나타내었는데, 이는 거칠기가 더 큰 경우 거칠기 손상으로 인한 암석 비지의 발생량이 많아져 화학 작용의 영향을 더 많이 받기 때문이다. 다만, 본 연구에서의 SHS실험은 900초 이내의 비교적 짧은 멈춤 시간을 적용하였기 때문에 화학 작용이 충분히 활성화되었다고 보기에는 어렵다. 이로 인해 마찰회복률의 차이가 크게 나타나지는 않은 것으로 판단되며, 추후 멈춤 시간의 증가에 따른 물-시멘트 간 화학적 특성 변화에 대한 연구가 보완된다면 유의미한 결론 도출이 가능할 것으로 판단된다.
Fig. 12는 추가적인 분석을 위해 모든 조건에서의 실험 결과를 함께 도시한 것이다. 여기서 유효 수직응력이 10 MPa 이상인 경우에 거칠기가 작은 시험편들의 역학적 조건(M-L)과 거칠기가 큰 시험편들의 수리-역학적 조건(HM-H)의 A값 차이가 크게 나타나지 않음을 확인할 수 있다. 실험 데이터의 부족으로 인해 직접적인 비교는 불가능하였지만, 동일한 거칠기에서는 더욱 차이가 작아질 것으로 예상해 볼 수 있다. 이는 높은 유효 수직응력 하에서는 실험 조건(역학적/수리-역학적)의 차이로 인한 화학 작용의 영향보다 유효 수직응력의 작용으로 인한 접촉면적의 증가가 더 지배적인 영향을 미친다는 것을 의미한다.
5. 결 론
본 연구에서는 고준위방사성폐기물의 심층처분에 있어 천연방벽의 장기진화를 평가하기 위해 요구되는 암반 절리의 마찰회복 거동을 분석하였다. 특히, 지하수와의 연계로 인해 중요시되는 수리-역학적 조건 하에서 실험을 수행하여 결과를 제시하였다. 서로 다른 거칠기를 지니는 시멘트 모르타르 시험편을 이용하여 절리면이 건조(dry) 상태인 역학적 조건과 젖은(wet) 상태인 수리-역학적 조건으로 나누어 SHS 실험을 수행하였으며, 이를 통해 도출한 주요 결과들을 요약하면 다음과 같다.
(1) 모든 실험 조건에서 절리면에 작용하는 유효 수직응력과 마찰회복률 A값은 서로 비례하는 결과를 보였으며, 이는 유효 수직응력의 증가가 절리면 접촉면적의 증가와 연계되기 때문이다. 따라서 절리면 접촉면적과 마찰회복률 또한 서로 비례관계에 있다는 것을 예상해 볼 수 있었다.
(2) 절리의 거칠기가 클수록 마찰회복률이 증가하는 경향을 보였으며, 이는 거칠기가 클수록 전단강도 이후 거칠기 손상이 크게 나타나 접촉면적의 변화가 증가하기 때문으로 판단되었다.
(3) 수리-역학적 조건에서는 역학적 조건에 비해 전반적으로 높은 마찰회복률을 나타내었다. 이는 수리-역학적 조건에서는 멈춤 시간이 길어짐에 따라 광물 용해와 같은 화학 작용이 활성화되어 접촉면적이 추가적으로 증가하기 때문으로 판단되었다.
(4) 수리-역학적 조건과 역학적 조건의 마찰회복률 차이는 거칠기가 더 큰 시험편에서 더 분명하게 확인되었다. 이는 거칠기가 더 큰 경우 거칠기 손상으로 인한 암석 비지의 발생량이 많아져 화학 작용의 영향을 더 많이 받을 수 있기 때문인 것으로 판단된다.
(5) 높은 유효 수직응력(10 MPa 이상)이 작용하고 있을 때에는, 실험조건(역학적/수리-역학적)의 차이로 인한 화학 작용의 영향보다는 유효 수직응력의 작용으로 인한 접촉면적의 증가가 더 절리의 마찰회복 거동에 지배적인 영향을 미치는 것으로 분석하였다.
이러한 결과들은 천연방벽 암반 절리의 마찰회복 거동을 파악하는 데 유용한 기초자료로 활용될 수 있을 것으로 기대된다. 하지만, 본 연구에서의 SHS 실험은 경사진 절리를 포함한 원형 시료를 대상으로 삼축압축 조건에서 수행되었기 때문에 절리면에 작용하는 수직응력이 실험 중에 일정하게 유지되지 않았다는 한계가 있다. 또한 정량적인 비교분석을 수행하기에는 시험편의 개수가 부족하였으며, 이로 인해 추가적인 실험이 요구된다. 추후 다양한 조건 하에서 추가 실험을 수행함과 더불어 직접전단조건 하에서 물을 주입하는 시스템을 갖추어 결과를 비교분석 한다면 유의미한 결과를 도출할 수 있을 것으로 판단된다.