1. 서 론
TBM (Tunnel Boring Machine)에 사용되는 굴착도구인 디스크커터는 암반을 파쇄하면서 세 방향의 절삭력(수직력, 회전력, 측력)을 받으며, 이러한 디스크커터의 절삭력은 무결암의 물성(일축압축강도, 간접인장강도, 파괴 인성 등), 암반 파라미터(불연속면의 물성, 풍화정도 등), TBM의 운용조건(굴진속도, RPM 등)과 밀접한 상관관계를 갖는 것으로 이해되고 있다. 따라서 이러한 디스크커터의 절삭력은 TBM의 설계와 굴착성능을 최적화하기 위하여 활용된다. 현재까지는 TBM의 굴착데이터는 추력, 토크와 같이 장비 전체 측면에서 측정되는 것이 보다 일반적이나 개별디스크커터의 회전속도, 온도, 마모량, 절삭력 등을 실시간으로 측정하고자 하는 연구도 지속적으로 수행되어 왔다(Entacher et al., 2012, Edelmann and Himmelsbach, 2013, Lan et al., 2016, Huang et al., 2022). 개별디스크커터의 굴착정보를 실시간으로 획득할 수 있는 경우, 지반상태에 대한 분포와 굴착상황을 보다 상세히 제공할 수 있으며 이는 TBM의 효율적인 운용에 도움을 줄 수 있다. 특히 TBM의 경우에는 NATM공법과는 달리 굴진면을 관찰하는 것이 매우 제한적이기 때문에 관측이 불가능한 영역의 지반상태를 파악하는 측면에서 매우 유용하다.
디스크커터에 의한 암반의 파쇄는 커터의 관입에 의하여 적정수준의 응력이 가해져야 이루어질 수 있으므로, 디스크커터에 가해지는 작용하중은 커터로 인한 암석의 절삭 및 굴착이 정상적으로 이루어지고 있는지를 모니터링하기 위한 중요한 정보를 제공하는 항목이라고 할 수 있다. 특히 세 방향의 절삭력 중 회전력의 경우, 커터의 회전과 밀접한 관련을 갖기 때문에 커터의 마모에 따른 회전 불능 등을 판별하는 중요한 데이터가 될 수 있다. 이러한 경우 디스크커터의 하중계측은 교체가 필요한 디스크커터를 판별하는 데 간접적인 정보로 활용될 수 있을 것이다. 상술한 바와 같이 디스크커터의 다양한 계측항목 중 절삭하중은 TBM의 굴진성능 및 디스크커터의 교체관리 측면에서 중요한 정보로 고려되고 있으나, 디스크커터가 설치되는 커터헤드 주변은 계측센서를 설치하기 위한 공간이 매우 협소한 점, 커터의 교체공정에 영향을 주지 않는 계측시스템의 적용이 요구되는 점, 높은 수준의 충격하중이 견딜 수 있는 센서가 필요한 측면에서 극복해야 할 사항이 많은 것으로 이해되고 있다.
TBM 본체에 발생하는 진동 등의 간접적인 파라미터를 통해 절삭하중을 추정하는 방법을 제외하고, 직접적인 계측방법은 디스크커터 주변에 로드셀 혹은 압력센서를 설치하는 방법과 변형률게이지를 설치하는 방법 두 가지로 구분되는 것으로 조사되었다. 본 기술보고에서는 현재까지 문헌을 통해 보고되고 있는 디스크커터의 하중계측에 관한 대표적인 연구사례를 소개하고자 한다.
2. 디스크커터 실시간 하중측정을 위한 연구현황
2.1 하중(압력) 센서를 이용한 계측 사례
디스크커터의 절삭하중을 직접적으로 측정하기 위해서는 통상 로드셀(load-cell), 압력센서와 같은 하중 혹은 압력을 측정하기 위한 센서가 필요하다. 이러한 측정장치들은 디스크커터의 내부 부품(베어링, 샤프트, 커터링) 혹은 커터하우징 내부에 설치되어야 하며, 센서가 설치되는 위치는 커터에 작용하는 하중이 직접적으로 전달되는 위치여야 하므로 센서를 설치할 부품과 위치를 결정하는 것이 매우 중요하다. 따라서 관련된 선행연구들을 살펴보면, 하중 계측센서의 적절한 설치 위치를 결정하기 위한 예비 실험실 시험을 수행하거나 수치해석을 통해 설치 위치의 적합성을 검증하는 단계를 거치는 것을 알 수 있다. 다른 고려사항으로는 계측센서에 연결되는 데이터 및 전원 공급케이블의 설치 방법이다. 디스크커터의 하중계측을 위해 연결되는 여러 케이블들은 디스크커터의 교체작업에 영향을 주지 않아야하며, 디스크커터가 교체되더라도 지속적으로 사용할 수 있도록 교체 측면에서의 편의성이 중요하다.
Entacher et al.(2012)의 연구에서는 커터하우징 내부에 위치하는 볼트에 두 종류의 로드셀(볼트 일체형, 와셔형)을 설치하는 방법을 적용하였다. 와서형은 볼트에 체결되는 중공형의 로드셀을 의미하며, 볼트 일체형의 경우에는 볼트 내부에 로드셀과 동일한 구조를 갖는 풀브릿지 스트레인게이지가 설치된 것을 의미한다. 해당 연구에서는 Fig. 1과 같은 유한요소해석을 통해 센서의 배치위치를 검토하여 적합한 센서의 설치위치를 결정하였다. 디스크커터의 절삭력이 직접적으로 잘 전달되는 커터하우징 및 볼트의 위치를 선별하고자 한 것으로 판단된다. 수치해석 결과를 통해 외부에서 가해진 하중(절삭력)에 대한 두 가지 측정 볼트의 반응이 올바르게 나타난다는 것을 확인하였고, 최종적으로는 센서의 설치 환경과 현장조건 등을 고려하여 Fig. 2와 같은 형태의 하중계측센서를 최종적으로 제안하였다. 이후 개발된 시스템의 적용성을 평가하기 위한 예비시험이 계획되었으며, 모든 센서들은 커터하우징에 설치되어 디스크커터의 교체에 영향을 미치지 않도록 고안한 것으로 보고하였다. Fig. 3은 전체적인 하중계측시스템의 개념도와 예비시험에서 구현된 사진을 보여준다.
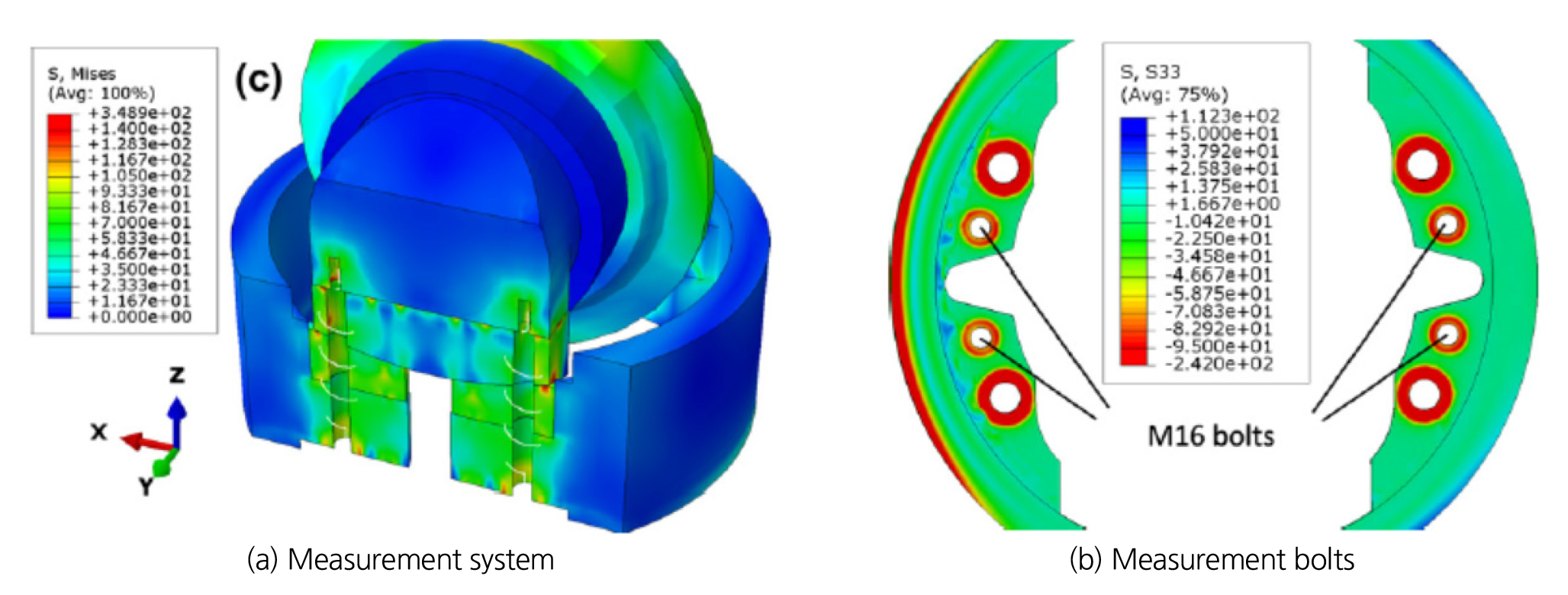
Fig. 1
Results of stress distribution of disc cutter housing from numerical simulation (Entacher et al., 2012)
Fig. 3(a)에 나타낸 하중계측시스템과 실내시험을 적용하여 하중센서의 계측정확도를 평가하기 위한 시험이 수행되었다. Fig. 4와 같은 디스크커터의 세 방향 절삭력(수직력, 회전력, 측력)에 따른 센서의 반응정도를 평가하기 위하여, 세 방향 분력이 독립적으로 작용하는 경우와 동시에 작용하는 경우로 나누어서 시험을 수행하였다. Fig. 5(a)에 나타난 바와 같이 수직력만 가해지는 경우에는 디스크커터가 축방향으로의 하중만 받는 경우와 Fig. 5(b)와 같이 디스크커터가 기울어져(11°) 회전력(FR)과 측력(FS)이 가해지는 경우로 구분된다.
Fig. 6은 제안된 실험실시험에서의 제안된 하중측정시스템의 적용 결과를 나타낸 것이다. MTS 압축시험기를 통해 입력된 하중신호(FMTS)와 볼트와 와셔형 로드셀을 통해 측정된 결과(△F)가 시간의 흐름에 따라 비교되어 있다. 로드셀을 통해 측정된 결과는 시험 전 초기 보정이 완료된 후 외부에서 가해진 하중에 따라 계측된 값이며, 외부의 하중과 절대적인 값이 일치하지는 않기 때문에 외부에서 가해진 하중의 파형과 로드셀을 통해 계측된 하중의 파형이 얼마나 일치하는지를 비교하여 센서의 계측정확도를 평가하게 된다. Fig. 6(a)에는 0°(수직력만 가해진 경우)에 대한 시험결과를 보여주고 있는데, 이들의 연구에서는 와셔형 로드셀의 경우에 측정센서에서 계측된 하중은 하중기를 통해 입력된 파형을 충분히 잘 나타내는 것으로 볼 수 있으나 상대적으로 볼트형 로드셀의 결과가 더 우수하여 추가적인 시험을 수행하지 않은 것으로 보고하였다. Fig. 6(a)와 같이 기울어진 각도가 없는 경우에는 모든 계측볼트의 반응정도가 유사하게 나타났지만, Figs. 6(b)-(d)의 결과와 같이 하중을 가하는 각도가 기울어진 경우에는 주어진 하중에 대한 볼트의 반응 정도가 다르게 나타났다. 주어진 시험조건에서는 4개 볼트의 측정 위치 중 3번(Bolt3)과 4번(Bolt4)의 반응성이 1번과 2번에 비해서는 우수하다는 결론을 얻었는데, 이는 계측시스템이 기울어진 방향과 관계가 있을 것으로 판단된다. 이와 같이 개발된 계측시스템은 실험실에서의 보정을 거친 후, 실제 TBM에 설치되어 현장적용성을 검증하였다. 오스트리아의 Koralm tunnel에 투입된 직경 9.93m의 쉴드 TBM (Aker Wirth GmbH사)에 적용되었으며, 계측시스템은 총 세 개의 위치(face cutter)에 설치되었다. Fig. 7은 세 개의 위치(중심에서부터의 거리에 따라 inner→ middle→ outer)에서 획득된 디스크커터의 절삭력의 예시를 보여준다. 비록 하중측정시스템을 통해 측정된 값을 검증할 수 있는 대조군은 없었지만, TBM의 총 추력 및 토크를 바탕으로 추정된 개별 디스크커터의 절삭하중의 범위와 상호비교하였을 때, 하중측정시스템을 통해 측정된 값은 합리적인 범위에 존재하는 것으로 보고하였다.
2.2 변형률 게이지를 이용한 계측 사례
앞선 사례에서는 디스크커터의 절삭하중을 직접적으로 측정하기 위해 하중 혹은 압력을 측정하기 위한 센서를 이용한 사례를 소개하였다. 이와는 달리 디스크커터의 작용하중 측정을 위해서 디스크커터의 내부부품 혹은 디스크커터 하우징에 변형률게이지를 설치하는 방식도 많이 적용되고 있다. Rostami(2013)은 TBM의 굴착성능 및 디스크커터의 절삭하중 추정을 위한 반이론적모델인 CSM모델의 개발을 위해 커터링에 스트레인게이지를 설치하여 절삭력을 획득한 사례를 소개한 바 있으며(Fig. 8), 국내에서도 일련의 연구(Chang et al., 2012, Chang et al., 2013, Choi et al., 2013)에서 스트레인게이지를 활용하여 절삭시험 중 발생하는 절삭력을 측정한 바 있으나 해당 연구는 변형률 측정을 통해 디스크커터 소재의 성능을 검증하는 목적이었다(Fig. 9). 변형률게이지를 이용하는 방식은 측정되는 변형률을 통해 하중을 역계산하는 방식으로, 재료의 물성을 알고 있고 또한 균질한 재료로 부품들이 이루어져 있는 경우에 적용이 용이하다. 하지만 재료의 물성이나 측정환경이 변화하는 경우에는 산출되는 응력(하중)값이 달라질 수 있으므로 비교적 부품의 물성변화가 없고 측정환경이 변화하지 않는 곳에서 계측을 수행하여야 한다. 이러한 측면에서 커터링에 스트레인게이지를 부착하는 방식은 현장에서 디스크커터의 절삭하중을 측정하기에는 한계가 있다고 볼 수 있다.
최근에는 변형률게이지를 하중센서와 동일하게 커터하우징 내부에 설치하여 디스크커터의 절삭하중을 측정하고자 하는 연구사례들이 소개되고 있다. Huang et al.(2022)의 연구에서는 Fig. 10과 같이 변형률 게이지를 디스크커터와 커터하우징의 연결부품에 부착하여 디스크커터의 절삭하중을 측정하고자 하였다. 스트레인게이지는 Fig. 10에 나타나있는 C-shape cushion block의 측면과 하부면에 설치되었는데, 세 방향의 절삭하중 축과 일치하도록 설치한 것으로 보인다. 또한 Fig. 11에 나타낸 실대형 회전식 절삭시험을 통해 계측시스템에서의 변형률과 응력과의 관계식을 도출한 것으로 보고하였다.
일련의 실험실에서의 검증작업을 마친 디스크커터의 하중계측시스템은 중국 Gaoligongshan 터널 건설공사에 투입된 직경 9 m의 그리퍼 TBM에 적용되어 현장적용성을 평가하였다. Fig. 12는 계측시스템이 설치된 위치와 스트레인게이지가 부착된 계측시스템의 사진을 보여준다. 주요 계측결과는 다음과 같다. 수직력의 경우에 50~800 kN의 크기로 측정되었고, 수직력의 크기는 측력에 비해 6~7배의 크기를 나타내었다. Fig. 13과 보여진 바와 같이 계측된 수직력은 0~300 kN의 범위에 집중된 경향을 보였고, 평균 수직력은 182 kN이었으며, 중위값은 165 kN라고 보고하였다. 해당 굴착구간에서 암반의 일축압축강도는 30~250 MPa였는데, CSM모델 또는 기존의 연구사례들(Rostami and Ozdemir, 1993, Rostami, 1997, Tumac and Balci, 2015)과 비교하여 합리적인 계측결과인 것으로 평가되었다.
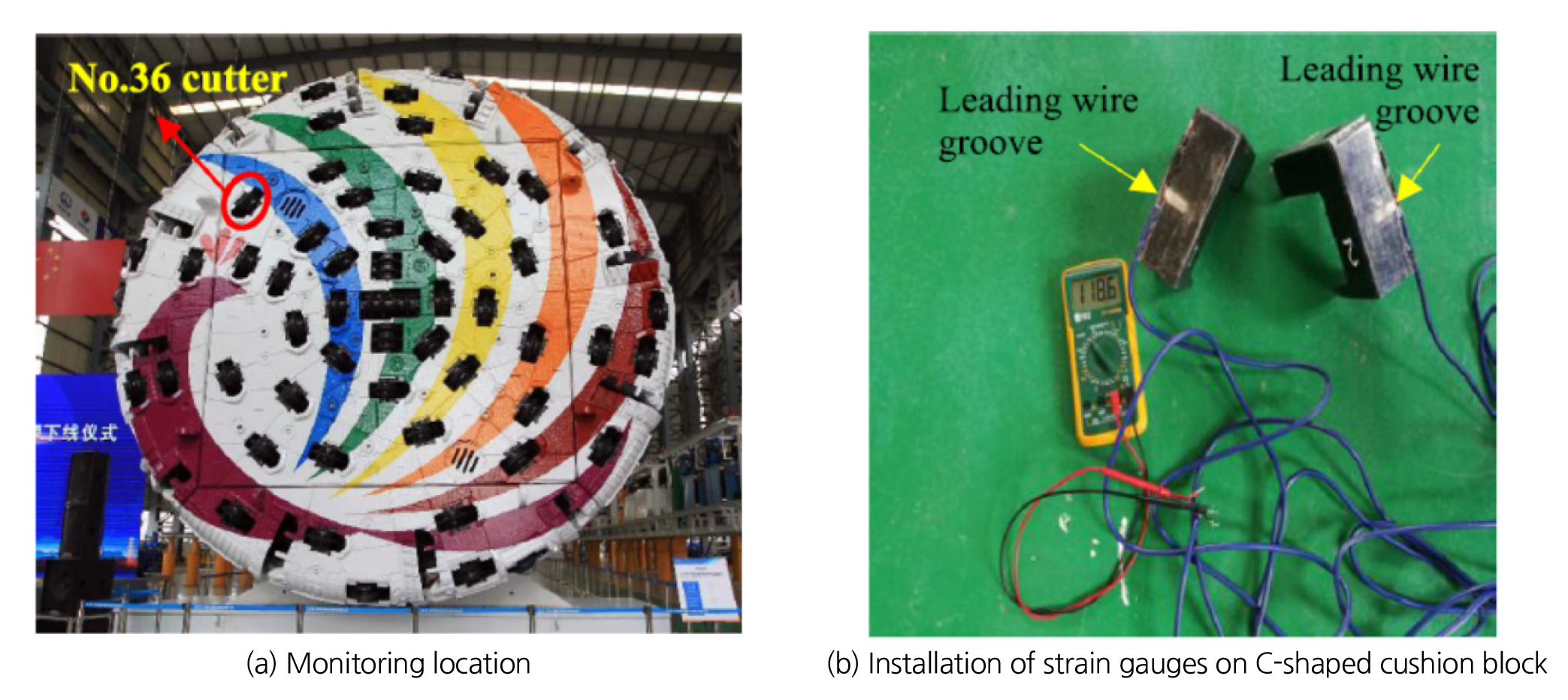
Fig. 12
In-situ real-time cutting force monitoring system for the cutter in the Gaoligongshan Tunnel (Huang et al., 2022)
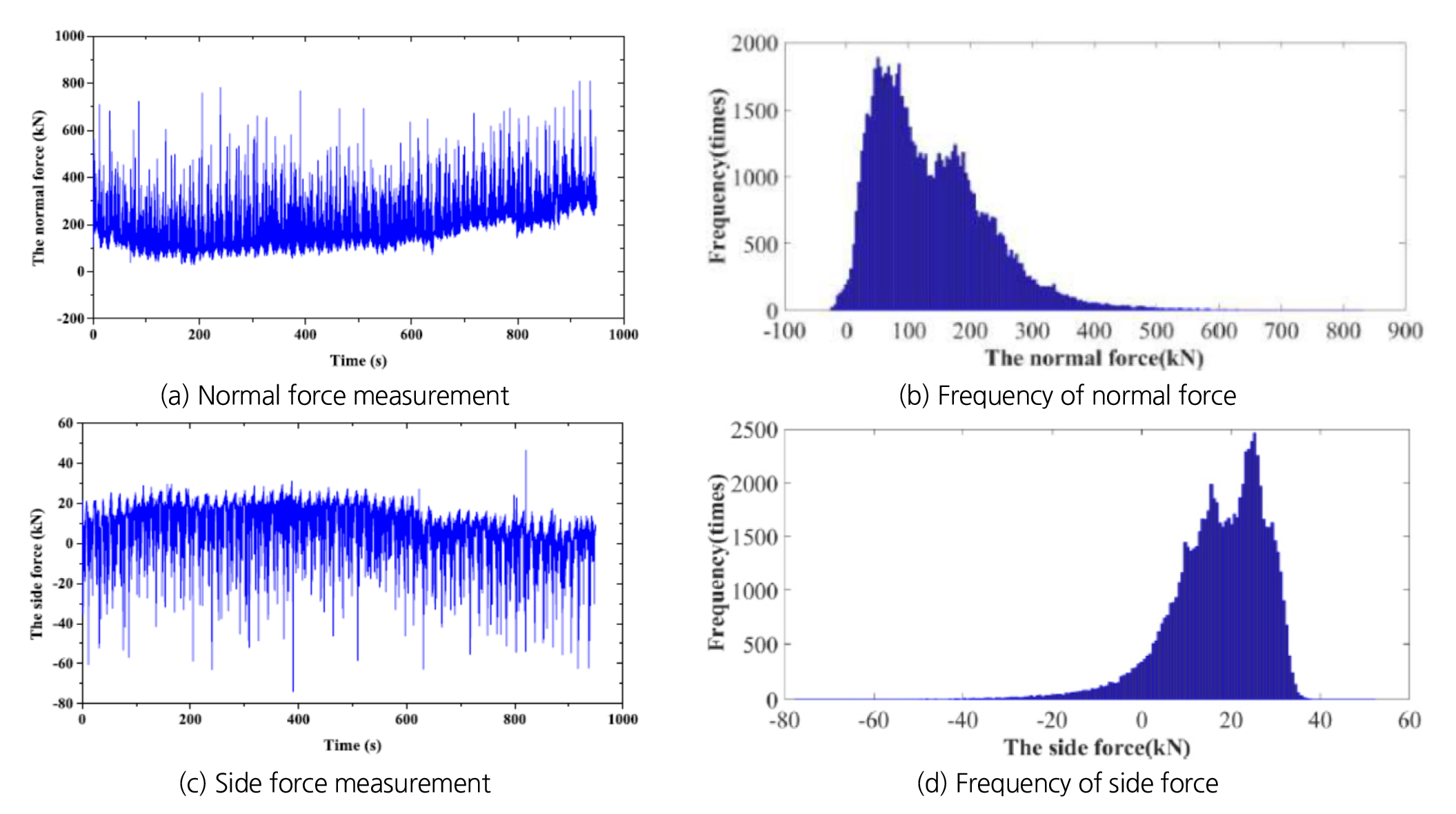
Fig. 13
Measurement result of disc cutter force monitoring system in the Gaoligongshan Tunnel (Huang et al., 2022)
3. 토 의
이상에서 살펴본 연구 사례에서는 로드셀 및 변형률게이지를 통해 디스크커터의 굴착도중 발생하는 절삭하중을 실시간으로 계측하고자 하였으며, 대체적으로 성공적으로 절삭하중을 계측할 수 있었던 것으로 평가된다. 하지만 이러한 실시간 디스크커터 하중계측시스템이 일반적으로 활용되기 위해서는 극복해야 할 부분들이 많을 것으로 판단되며, 다음과 같은 사항들을 고려할 필요가 있을 것으로 판단된다. 먼저, TBM 제조사 별로 각기 다른 면판과 디스크커터의 하우징의 형상을 적용하고 있고, 또한 디스크커터를 하우징에 체결하는 방식이나 부품의 형상이 서로 다르다. 따라서 제안된 시스템들을 모든 제조사의 TBM에 적용하기에는 현재 방식은 한계가 있을 것으로 추정된다. 또한 상술한 연구사례에서의 계측시스템의 형태를 통해 알 수 있듯이 계측시스템을 커터헤드에 설치하기 위해서는 커터헤드 혹은 커터하우징의 가공이 필수적이다. 소개된 연구사례에서는 일부 디스크커터에만 측정시스템이 적용되었으나, 이러한 시스템이 상용화되는 경우에는 모든 디스크커터에 설치될 가능성이 높다. 이러한 경우 하중계측시스템의 설치 뿐만 아니라 계측되는 데이터를 전송하기 위한 통신선, 전원케이블을 매설하는 작업 또한 커터헤드의 형상과 매우 밀접한 관련이 있고, 계측된 데이터를 후방에서 전송받기 위한 통신매체 설치, PLC와의 통신설정 등도 계측시스템의 적용 시에 필히 고려해야할 사항으로 분석된다.
4. 결 론
본 기술보고에서는 상술한 바와 같이 디스크커터의 절삭하중을 실시간으로 측정하기 위한 계측시스템의 개발현황에 대해서 살펴보았다. 해외의 연구사례에서는 하중센서(로드셀)과 변형률게이지를 활용하여 디스크커터의 절삭하중을 측정하기 위한 시스템의 개발을 진행하고 있으며, 실제 현장에서의 적용성도 우수하게 평가된 것으로 보여진다. 하지만 이러한 하중계측시스템이 상용화되기 위해서는 현실적으로 극복해야 할 사항들이 많은 것으로 판단되며 이에 대해서는 지속적인 연구가 필요할 것으로 판단되었다. 본 기술보고에서 소개한 계측시스템들은 TBM 작업 중 커터의 교체 과정에 방해가 되지 않도록 고안되었으나, 일부 영역의 커터에만 적용이 되었으므로 모든 디스크커터에 적용이 되는 경우 센서의 설치, 보호, 통신 및 전원 케이블의 설치 등에 있어 부차적으로 고려해야 할 사항이 있으므로 이에 대해서는 추가 연구가 필요할 것이다. 향후 이러한 디스크커터의 실시간 하중계측시스템이 활용되는 경우 TBM의 굴진성능을 실시간으로 평가하거나, 전방의 지질조건을 상세히 분석하는데 유용한 정보를 제공할 수 있으며, 손상된 커터의 감지가 가능하고 커터 및 커터헤드 설계에 대한 기본적인 정보를 제공하는데에도 도움이 될 것이다. 이러한 원격 커터 모니터링 기술은 점점 중요도가 증대하고 있으며, TBM 터널링 분야에서 큰 가치를 지닐 것으로 기대된다. 향후 국내에서도 이를 위한 관련 연구가 수행되기를 기대한다.