1. 서 론
2. 디스크커터 계측 센서의 종류
2.1 초음파센서(Ultrasonic wave sensor)
2.2 와전류센서(eddy-current sensor)
2.3 자기센서(Magnetic sensor)
3. 디스크커터 마모계측 연구현황
3.1 초음파센서 적용 사례
3.2 와전류센서 적용 사례
3.3 자기센서 적용사례
3.4 계측데이터의 통신 방법
4. 결 론
1. 서 론
TBM에 장착되어 암석을 절삭하는 디스크커터는 암반을 굴착하는 과정에서 마모나 손상이 발생하며, 과다하게 마모가 이루어지거나 파손된 경우에는 절삭효율이 저하되거나 암석의 절삭이 불가능하므로 적절한 시기에 교체하는 것이 중요하다고 할 수 있다. 통상 디스크커터의 마모량과 커터의 소모개수를 추정하기 위한 방법으로는 일련의 마모지수시험과 석영함유량과 같은 암석물성을 이용하는 경험적인 예측방법(Gehring, 1995, Bruland, 1998)이 주를 이루고 있으나, 이러한 암석의 물성을 이용하여 커터의 소모량을 추정하는 방법은 디스크커터의 정상마모를 가정하기 때문에 실제 현장에서 나타나는 디스크커터의 다양한 마모나 손상형태를 고려하여 커터의 교체관리에까지 활용되기에는 한계가 있다고 할 수 있다(Farrokh and Kim, 2018). 따라서 디스크커터의 교체시기를 판별하기 위해서는 현재까지 디스크커터의 교체시기를 판별하기 위해 인력에 의한 계측이 주로 이루어지고 있다. 작업자가 커터헤드 챔버 내로 진입하여 마모량을 측정하기 위해 제작된 자 혹은 가이드 등을 이용하거나, 육안 검사를 통해 교체가 필요한 손상된 커터를 판별하고 있는 상황이다. TBM 챔버 내부는 토사나 지하수의 유입 가능성이 항상 존재하고, 고압 등의 위험한 환경에 노출될 가능성이 높아 안전에 대한 이슈가 항상 존재한다. 이를 위해 챔버 내에서 작업하는 작업자는 이러한 환경에 적응하기 위한 특수 훈련을 거치기도 하고, 각종 안전장비(잠수복, 산소장치 등)를 작용한 상태로 작업을 수행하고는 있지만 작업 도중 인명사고의 위험성은 항상 존재한다고 할 수 있다.
대구경 TBM의 경우에는 커터의 교체작업에서의 안전 관련 문제를 극복하기 위하여 로봇 등 최신 기술을 접목한 커터의 자동교체 시스템에 대한 기술개발이 이루어지고 있다(Yuan et al., 2019, Du et al., 2022). 하지만 이러한 최신 시스템들은 아직까지 상용화하기에는 기술개발이 더 필요한 것으로 판단되고 있으며, 매우 고가의 시스템일 것으로 추정된다. 또한 전력구, 공동구와 같은 소-중구경 TBM 장비에는 기술의 적용을 위한 장치를 설치하기 위한 공간이 제한적이며 재활용되고 있는 기존에 제작된 장비들에는 적용하기가 어렵다는 한계점도 가지고 있다. 이러한 커터의 교체 작업의 자동화와는 별개로 상술한 바와 같이 커터의 마모정도나 손상 상태를 판별하기 위해서는 일정한 주기마다 커터의 계측이 필요한 상황이기 때문에 커터의 계측으로 인한 작업자의 안전과 관련된 이슈가 존재할 뿐만 아니라 커터의 계측을 위해서는 커터헤드 챔버를 비우는 작업과정이 필요하기 때문에 다운타임(downtime)이 증가하고 막장면의 안정성이 저하되는 등의 시공상의 문제점도 발생할 수 있다.
이러한 커터 계측과 관련한 여러 한계점들을 극복하고자 해외의 장비제작사를 중심으로 디스크커터의 상태를 각종 센서를 활용하여 계측하고 모니터링 하기 위한 연구들이 수행되어 오고 있는 것으로 보고되고 있다. 본 기술보고에서는 해외에서 개발이 진행되고 있는 디스크커터의 마모량 계측기술에 대하여 소개하고자 한다. Herrenknecht, Robbins 등 해외의 유수 장비 제작업체에서 기술개발을 활발하게 진행하고 있는 것으로 조사되었다. 디스크커터의 마모계측을 위한 센서로는 초음파센서(Ultrasonic wave sensor), 와전류센서(Eddy-current sensor), 자기센서(Magnetic sensor)등이 활용되고 있는 것으로 조사되었는데, 각 계측기술의 마모량 계측 원리를 소개하고 각 센서들이 적용된 사례와 기술의 개발 현황 등을 조사하여 요약하였다.
2. 디스크커터 계측 센서의 종류
2.1 초음파센서(Ultrasonic wave sensor)
초음파센서는 파의 속도와 이동시간을 기반으로 탐지하고자 하는 물체와의 거리를 판별하는 원리를 사용하며 Fig. 1은 초음파 센서의 계측원리를 나타내는 개요도이다. 초음파 두께 측정은 초음파 변환기에서 방출한 파가 매체의 경계면에 도달하고, 경계면에 도달한 파는 매체의 경계면에서 반사가 된다. 반사된 파동은 초음파 변환기로 다시 돌아오고, 초음파 변환기는 파동을 전기 신호로 바꾸는 원리이다. 식 (1)과 같이 파가 전파되는 매체에서 속도(v)와 측정시간(T)를 이용해 거리(L)를 계산한다. 초음파 센서는 상대적으로 설치가 간단하고 편하다는 장점이 있지만, 변위계측 용도로는 다른 센서와 비교하여 상대적으로 측정 정밀도가 높지 않은 것으로 알려져 있다. 초음파 센서를 이용한 거리측정은 로봇 공학 등에서 근접한 물체를 정확하게 인식하기 위해 사용되거나, 연속 측정을 하기 위해 사용하는 모니터링 시스템인 차량감지 시스템과 같은 거리 측정, 질병 진단과 치료 등 거리 정보에 기반한 기술에 많이 활용되고 있다.
2.2 와전류센서(eddy-current sensor)
와전류(eddy-current sensor)는 전자기유도현상을 응용한 것으로 도체에 발생하는 와전류에 의한 코일의 인덕턴스 변화를 이용한 센서를 말한다. Fig. 2(a)는 와전류센서 주변에서 발생하는 전자기현상을 개략적으로 나타낸다. 코일 내부에 흐르는 교류전류에 의해 코일 주변에는 고주파 교대 자기장(1차 자기장)이 생성되는데, 이 자기장은 도체의 표면층에 와전류를 생성시킨다. 1차자기장에 의해 생성된 와전류에 의해 도체의 표면층에는 다시 2차자기장이 생성되며, 이 2차자기장의 생성방향은 1차자기장과는 반대의 방향으로 작용한다. 이러한 자기장의 상호작용으로 발생하는 코일의 매개변수와 인덕턴스 변화를 측정하는 것이 와전류센서의 원리이다. 이러한 과정을 교류전원, 코일과 도체의 저항, 상호 인덕턴스로 구성된 전기회로로 표현하면 Fig. 2(b)와 같다. R1은 코일의 저항, L1은 코일의 인덕턴스, R2는 측정 물체의 등가 저항, L2는 측정 물체의 등가 인덕턴스 , M은 코일과 측정 물체 간의 상호 인덕턴스를 의미한다. 인덕턴스는 회로에 흐르는 전류의 변화에 의해 전자기 유도로 생기는 역기전력의 비율을 나타내며 상호 인덕턴스 계수(M)은 로 나타난다. K는 코일과 도체 사이의 거리를 나타내는 값으로 거리가 멀어지면 K는 0에 수렴하게 되며 이에 따라 M도 0에 수렴하게 된다. 반면 코일과 도체 사이의 거리가 가까워지면 K값이 1에 수렴하여 M값은로 변화한다. 이러한 상호인덕턴스의 변화를 측정하는 것이 와전류센서를 이용한 거리계측의 기본원리에 해당하며, 이와 더불어 와전류는 비철 광석인 암석에 대한 강한 침투성을 가지고 있어 에너지 코일과 도체(디스크커터) 사이의 자기장 에너지를 이용하여 도체의 위치, 표면 형태, 두께 등을 측정 가능하게 한다.
2.3 자기센서(Magnetic sensor)
자기센서는 자기장 또는 자기력선의 크기와 방향을 측정할 수 있는 센서이다. 영구자석 또는 전자석 주변에 생성되어 있는 자기장의 영향으로 주변 물질의 성질이 변하는 효과를 이용하여 자기장의 크기와 방향 등을 측정할 수 있다. 일반적으로 자기센서로 활용되는 홀 효과(Hall effect)를 이용한 홀센서나 자기장의 영향으로 물질 내 전기저항이 변화하는 자기저항효과를 측정하는 자기저항(Magnetoresistive , MR)센서로 구분하고 있다(Fig. 3). 통상 자기센서를 통해 측정되는 값은 자기력 선속 밀도(Magentic flux density)이며, 디스크커터에 마모가 발생하게 되면 자기센서 주변에 설치된 자석과 디스크커터사이의 거리변화에 따라 자기력선속밀도가 변화하게 되고 이를 자기센서를 통해 측정하여 디스크커터의 마모량을 산출할 수 있다.
3. 디스크커터 마모계측 연구현황
3.1 초음파센서 적용 사례
초음파 센서가 디스크커터의 마모도 계측에 활용된 사례들이 일부 문헌을 통해 소개되고 있다(Guo et al., 2013, Edelmann, 2013). Guo et al.(2013)에서는 초음파센서를 통한 기술개발 내용을 그림 등을 통해 소개하고 있지 않으므로 본 논문에서는 대표적인 사례로 독일의 TBM 장비회사인 Herrenknecht사가 개발을 진행하고 있는 것으로 파악되는 계측시스템을 소개하고자 한다. Fig. 4는 Herrenknecht사에서 개발 중인 디스크커터의 실시간 마모계측 시스템을 나타낸다. Fig. 4(a)와 같이 초음파 센서를 TBM 하우징 내 커터 뒤쪽(굴착면 반대쪽)에 부착한 것으로 파악되며, 쉴드 TBM 챔버 내 환경에서의 검증을 위해 Fig. 4(b)와 같이 벤토나이트 이수액 내에서 실험을 진행한 것으로 보고하였다. Fig. 5와 같이 개발된 초음파센서 계측시스템에 의한 커터마모 계측결과는 상당한 정확도를 확보하고 있는 것으로 보고되고 있으나, 해당 시스템에 적용된 센서의 사양, 설치방법, 초음파 속도를 이용한 거리계산에 필요한 보정치들에 대해서는 자세한 내용들을 공개하지 않고 있는 상황이다.
초음파센서의 경우 계측원리가 직관적이고 측정이 간편하다는 장점이 있으나 현장조건 등을 감안하면 다음과 같은 사항들을 고려할 필요가 있을 것으로 보인다. 초음파 센서를 통해 방출되고 송신되는 초음파는 거의 모든 표면에서 반사되는 특징을 갖는다. 이러한 특성은 TBM의 굴착 시 커터 하우징 내로 유입 가능한 토사, 버력, 자갈 등의 유입에 의해 초음파 센서가 거리를 측정하는데 악영향을 미칠 수 있다는 것을 의미한다. 또한 초음파센서의 여러 유형 중 송신기와 수신기가 분리된 형태에서는 초음파센서의 측정값이 파의 입사각에 영향을 받게 되는데, Fig. 6(a)에서 보이는 것과 같이 센서가 물체에 수직으로 향하면 측정이 가장 정확하지만, Fig. 6(b)에서 보이는 것처럼 입사각이 너무 크게 되면 물체에서 반사된 파동이 수신기에 도달하지 않아 측정이 원활하지 않게 된다. 이에 따라 초음파센서의 계측값은 커터의 표면 상태에 영향을 받는다고 할 수 있다.
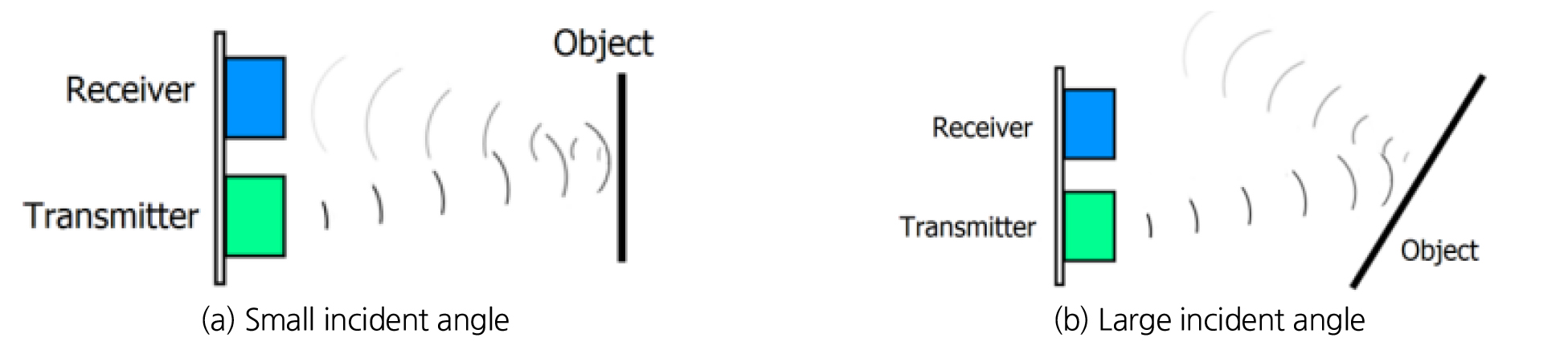
Fig. 6.
Differences in reflection behavior of ultrasonic wave according to incident angle (Zhmud et.al, 2018)
또한 초음파의 전파속도와 투과/반사 정도는 매질의 밀도, 체적탄성률, 음향저항 등에 의존적인 특성을 갖는다. TBM 챔버 내부에서 초음파 센서를 이용하여 마모도를 측정하기 위해서는 초음파가 지하수나 토사를 투과하여 커터까지 도달해야 하고, 커터에서 음파가 반사되어 수신기에 도달해야 한다. 이러한 과정에서 초음파는 송신기로부터 수신기로 돌아올 때 까지 다양한 매질을 통과할 수 있는데 이에 따라 초음파의 전파속도가 일정하지 않을 수 있으며, 전파속도를 고려한 계측 값의 보정이 디스크커터의 마모계측에서 매우 중요한 이슈가 될 것으로 볼 수 있다. 또한 초음파센서의 계측 성능은 음파가 통과하는 매질의 온도에 영향을 받는 것으로 보고되고 있으므로 이에 대한 고려가 필수적이다.
3.2 와전류센서 적용 사례
와전류센서를 디스크커터의 마모도 계측에 활용한 사례들도 해외문헌을 통해 일부 소개되고 있다(Lan et al., 2019, Wang et al., 2019). 초음파센서와 마찬가지로 와전류센서도 커터하우징(굴착면 반대쪽 혹은 하부)에 설치되며, 굴착이 이루어짐에 따라 발생하는 디스크커터의 마모량을 커터링과 센서 사이의 거리를 통해 측정한다. Fig. 7은 이러한 계측 원리를 개략적으로 나타낸 것이며, D1은 커터가 마모되기 전 측정된 거리이며 D2는 커터가 마모된 후 측정된 거리이다. 마모량 W는 D1과 D2의 거리 차이에 따라(D2 – D1)으로 나타난다.
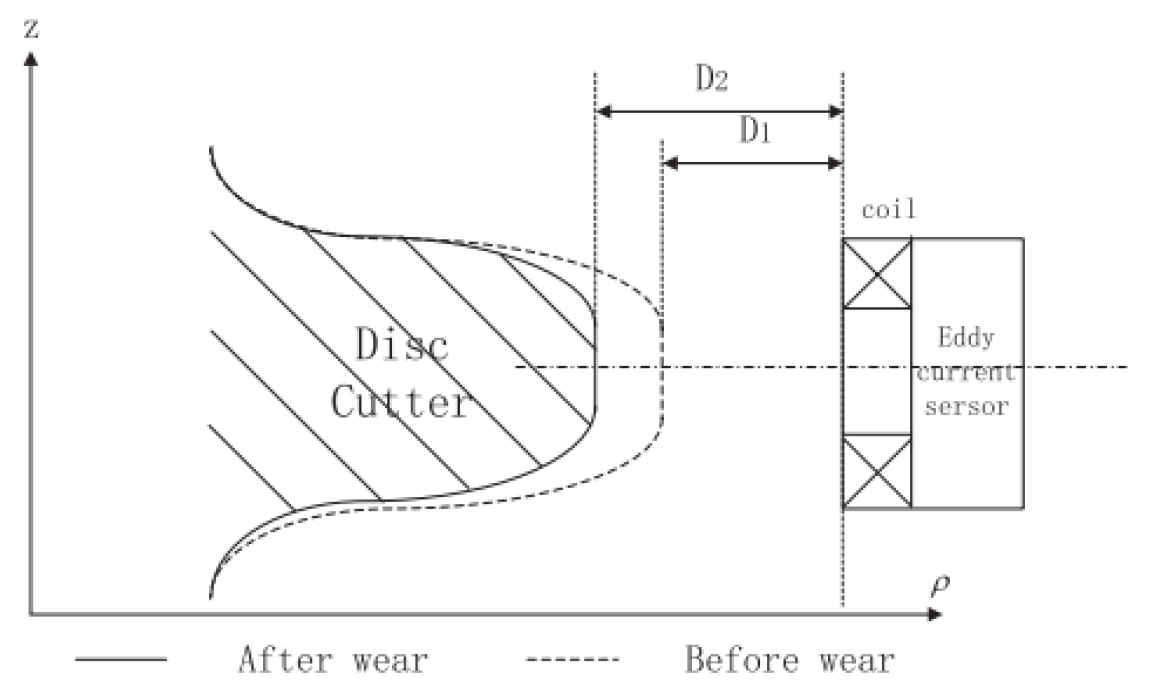
Fig. 7.
Schematic diagram of distance measurement between eddy-current sensor and cutter (Lan et al., 2019)
Lan et al.(2019)는 와전류센서를 이용한 디스크커터의 마모계측시스템을 소개하고 이를 중국의 Yinsong Tunnel에 적용한 사례를 소개하였다. 와전류센서를 통해 측정되는 계측값의 보정을 위해 수행된 일련의 실험실시험 내용을 소개하였고, 특히 센서와 디스크커터 사이에 암석이나 토사와 같은 지반재료가 위치하는 경우(Fig. 8), 이들의 영향을 고려한 계측값의 보정과 계측에러 값의 처리가 중요하다고 하였다. 보정된 계측시스템은 현장에 적용되기 전 선형절삭시험을 통해 암석을 절삭하는 도중에 측정되는 계측값의 정확도를 검증하였으며, 계측오차는 0.15 mm 수준인 것으로 보고되었다.
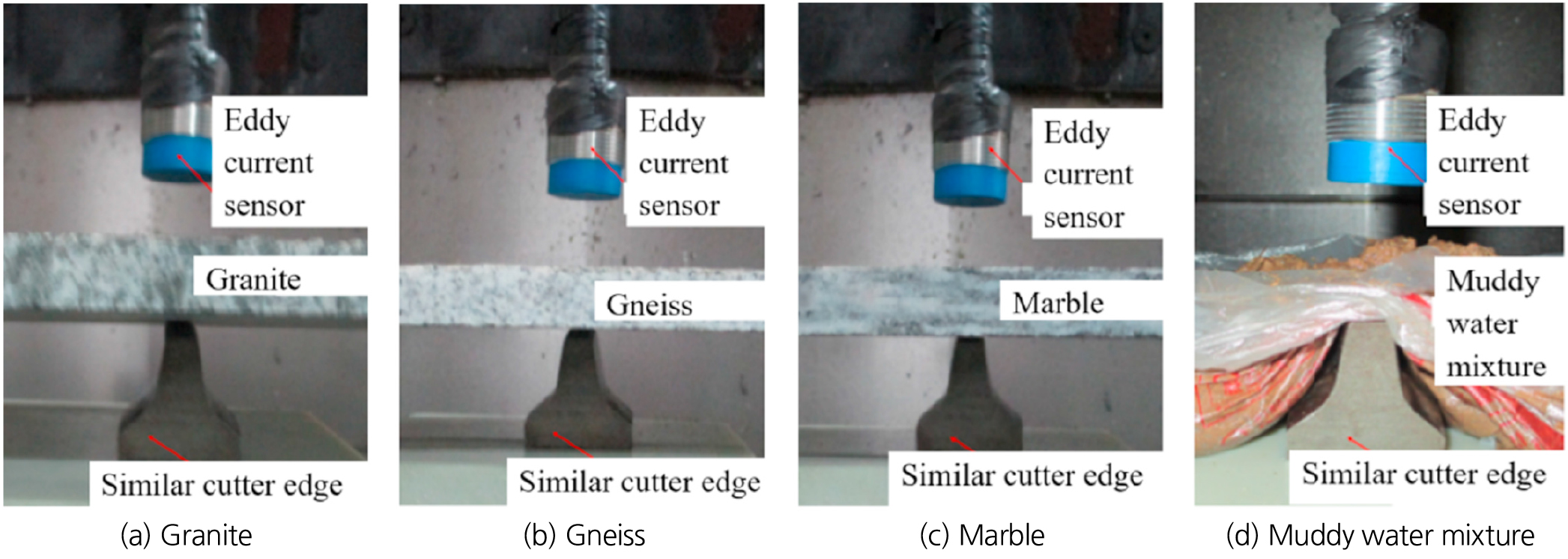
Fig. 8.
Laboratory test to calibrate the effect of media between cutter and eddy current sensor (Lan et.al., 2019)
실험실에서의 보정작업과 정확도 검증을 마친 계측시스템은 상술한 바와 같이 Yinsong 터널을 굴착하는 TBM에 시험 적용되었다. 해당 TBM의 직경은 7.95 m이며(Gripper TBM), 총 51개의 디스크커터(센터커터: 17인치, 페이스/게이지커터: 19인치)가 설치되었고 그중 센서가 설치된 디스크커터의 위치는 페이스커터 중 비교적 외곽에 위치한 29번과 37번에 설치하였다(Fig. 9(a)). 커터 마모측정 장치가 설치된 모습은 Fig. 9(b)과 같으며, 두 개의 센서 중 29번에 설치된 모습이다. 특히 계측자료를 무선통신을 이용하여 전송하였고 Fig. 10은 TBM에 적용된 전반적인 계측시스템의 구조를 나타낸다.
와전류센서를 통해 계측된 마모량은 특수 제작된 캘리퍼(정밀도 1 mm)로 측정된 총 8회의 실제값과 비교하여 그 성능을 확인하였고, 두 개의 계측지점에서 실시간으로 측정된 마모량과 실제 계측치를 비교하였을 때, 8회의 계측 중 최대 0.43~0.93 mm의 오차가 발생하였다고 보고하였다. 실제 마모량의 측정에 사용된 캘리퍼의 정밀도가 1 mm임을 고려할 때, 최대 오차값이 실제 센서의 성능을 그대로 나타낸다고는 볼 수 없지만 현장에서의 여러 열악한 상황을 고려하면, 본 현장에 적용된 와전류센서는 커터의 마모량을 비교적 실시간으로 잘 측정한 것으로 평가된다.
3.3 자기센서 적용사례
자기 센서를 적용하여 디스크커터의 마모량을 측정한 사례로는 중국에서 이루어진 연구(Gong et al., 2021)가 대표적이다. 상술한 바와 같이 자기센서의 종류는 홀센서와 자기저항 센서로 구분되며, 해당 연구에서는 Fig. 11과 같이 휘트스톤 브리지(Wheatstone) 회로 구조로 설계된 자기저항방식의 센서를 사용하였다. 4개의 자기 저항이 브리지 암에 있으며 저항이 자기장에 민감하기에 자기장의 변화에 따라 출력 전압이 변화하는 방식이다.
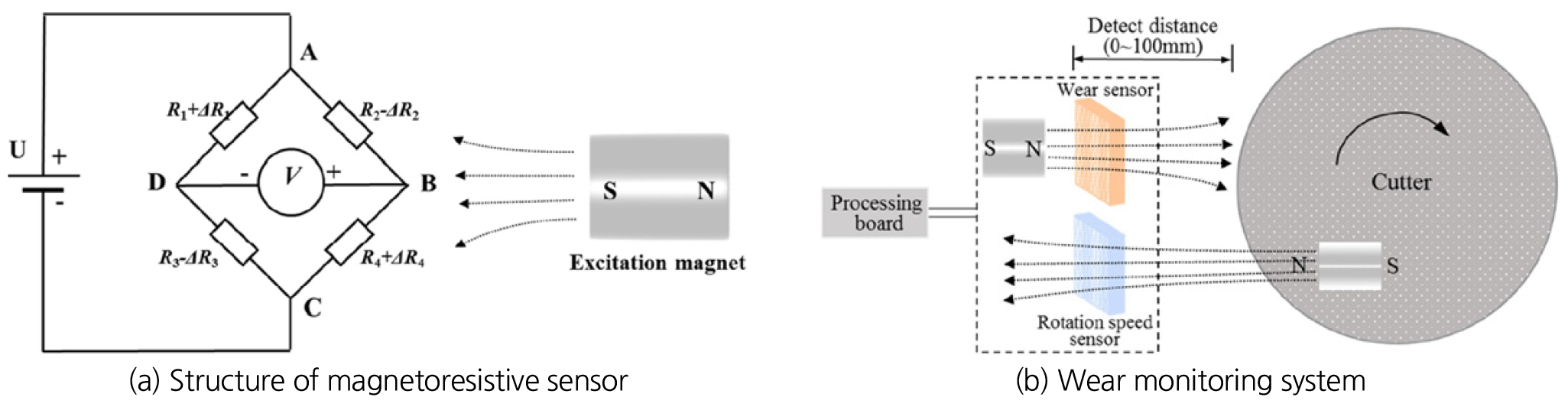
Fig. 11.
Structure of MR sensor and working principle of the cutter wear measurement system (Gong et al., 2021)
해당 연구에서는 공기, 물, 슬러리, 먹(muck) 총 네 가지의 매체에서 마모값에 대한 보정 곡선을 일련의 실내시험을 통해 획득하였으며, 실내시험 도중 센서는 Fig. 12와 같이 실제 작업 조건을 고려하여 고려된 매질에 의해 완전히 잠긴 상태를 유지하였다. 시험결과로 자기저항센서가 서로 다른 매질에 존재하는 경우에도 마모측정 값에는 큰 변화가 없음을 확인하여, 자기저항센서의 계측값은 센서주변에 위치하는 비자성 매질(굴착된 토사나 암석)에는 영향을 받지 않는다는 것을 의미한다.
Gong et al.(2021)은 Dadonghu 지역에 투입된 TBM 터널에서 개발된 계측시스템의 적용성을 평가하였다. 터널의 전체 길이는 1,612 m이며 직경 6.56 m의 EPB Shield TBM이 사용되었다. 최대 RPM은 3이고 최대 굴진 속도는 80 mm/min이다. 커터 헤드에는 30개의 디스크 커터와 26개의 스크래이퍼(scraper)가 장착되어 있으며 그 중 8개는 측면 스크래이퍼다. 디스크 커터의 직경은 15.5인치이고 커터의 둘레는 1250 mm이다. 커터 헤드의 서로 다른 위치에 있는 두 개의 커터가 시스템 모니터링을 위한 센서 설치 위치로 선정되었으며 설치 위치는 Fig. 13과 같다. 18번과 26번 커터를 선정한 이유는 최외곽부에 위치하는 커터가 마모가 많이 발생하기 때문일 것으로 판단되며, 게이지 커터(gage)와 페이스 커터(face cutter)를 각각 선정하여 결과 값을 비교한 것으로 보인다. Fig. 14는 본 현장에서 적용한 계측시스템의 전반적인 개요도를 나타내고 있다.
Fig. 15는 시험 구간에서 TBM의 굴착 도중 측정된 디스크커터의 마모계측 결과를 나타낸다. 총 1600 m(1343개링)에 걸친 계측이 이루어졌다(Gong et al., 2021). 26번 커터의 경우에는 커터의 마모가 지속적으로 증가하는 경향을 보이다가 1300번대 링을 통과하는 시점에서 계측 값이 14.6~25.1 mm 사이의 범위에서 불규칙하게 변동된 것으로 나타났는데, 계측값의 변동이 발생하기 이전의 마모량은 19.2 mm인 것으로 측정되었다. 26번 커터의 경우 장비의 유지보수 도중 실제 커터의 마모형태를 확인한 결과 Fig. 14의 좌측에 나타난 바와 같이 커터링의 편마모가 발생한 것으로 확인되었고, 평균적인 커터링의 마모량은 19.4 mm로 계측치와 매우 유사한 것을 확인할 수 있었다고 보고하였다. 반면 18번 커터의 경우에는 26번 커터와 같이 초기에 마모량이 증가하는 경향을 나타내다가 마찬가지로 1300번대 링 부근에서 계측값이 38 mm로 갑자기 증가하는 계측결과를 보여주고 있다. 이는 계측 센서의 측정 최대치가 38 mm이기 때문인데, 26번 커터의 경우에는 디스크커터가 파손되어 커터링의 탈락이 발생한 것으로 확인되었다. 이상의 결과를 통해 볼 때, 자기센서를 사용한 해당 마모계측시스템 또한 계측결과가 우수하게 나타난 것으로 판단된다.
3.4 계측데이터의 통신 방법
디스크커터의 마모량 계측을 위해서는 데이터를 정확하게 계측하는 것도 중요하지만 계측된 데이터를 효율적으로 후방의 데이터로거(data logger)를 통해 PLC (programmable logic controller)로 전송하는 것이 매우 중요하다. 물론 각종 센서로부터 계측되는 데이터를 가장 안정적으로 송수신하는 방식은 유선방식일 것이다. 하지만 커터헤드가 굴착 도중 지속적으로 회전하기 때문에 전선들의 꼬임을 방지하기 위한 별도의 장치(rotary joint 등)가 필요하고, 공간이 협소한 커터헤드 부의 특성상 설치공간이 제한될 가능성이 높다. 이러한 이유로 디스크커터의 각종 정보계측을 위한 선행연구(Guo et al., 2013, Lan et al., 2019, Gong et al., 2021)에서는 무선통신을 통해 유선통신의 한계점을 극복하려고 노력한 것으로 보인다. 무선통신을 적용하는 경우에는 각종 계측정보를 데이터의 전송과정에서 커터가 설치되어 있는 커터헤드로부터 챔버를 통과하는 과정이 가장 중요할 것으로 판단된다. 커터헤드 챔버 내부는 통신을 위한 전자파를 송수신하기에 어려운 환경일 가능성이 높기 때문이다. 디스크커터 주변에 설치되어 각종 정보를 계측하기 위한 센서가 위치하는 커터헤드는 환경적인 특성상, 센서 주변에 지하수, 벤토나이트 이수액, 굴착토사, 암버럭 등 다양한 매질이 위치할 가능성이 높다(Fig. 16). 특히 슬러리 및 토압식 쉴드 TBM의 경우, 굴착을 하는 도중에는 TBM 챔버가 압축공기, 이수액, 굴착토사 등의 혼합물로 채워져 있기 때문에 이러한 난환경에도 가능한 통신방법이 요구된다고 할 수 있다. 현재 각종 산업분야에서 활용되고 있는 무선통신의 종류로는 블루투스, 와이파이, 지그비, LoRa 등이 있으며, 각종 무선 통신모듈들은 통신 원리에 따라 전송거리, 소비전력, 전송속도, 보안성 등의 측면에서 차이가 있으나, 이러한 일반적인 정보들로 어떠한 통신방법이 커터헤드에서 측정되는 정보를 송수신 하기에 적합하다고 말하기는 어렵다. TBM 본체 내부의 환경 및 공간, 데이터를 후방으로 전송하기 위한 통신시스템, 센서와의 호환성, 보안 등을 복합적으로 고려하여 적합한 통신기술을 선정할 필요가 있을 것으로 판단된다.
4. 결 론
본 기술보고에서는 TBM 디스크커터의 실시간 마모계측을 위한 기초연구로써 해외문헌에서 소개하고 있는 디스크커터의 마모계측방법에 대하여 조사하여 각 계측기술의 기본원리, 기술개발현황, 현장적용사례 등을 소개하였다. 해외 문헌에서 공개하고 있는 디스크커터의 실시간 계측기술에 대하여 조사한 결과, 해외에서는 초음파, 전자기, 와전류센서를 이용하여 디스크커터의 마모도를 측정하고 있는 것으로 파악된다.
각 센서들은 측정원리에 따라 한계점과 장점을 가지고 있는 것으로 판단되나, 선행연구들에서는 개발된 측정시스템을 현장에 성공적으로 적용한 것으로 보고하고 있다. 하지만 각 센서들의 계측값에 의해 산출되는 커터마모량을 보정하기 위한 실내시험들이 자체적으로 수행된 것으로 조사되었으며, 이러한 결과들은 상세히 공개되어 있지 않다. TBM의 형식에 따라 센서가 설치되는 주변의 환경이 크게 변화할 수 있기 때문에, 센서 계측치를 보정하기 위한 작업은 TBM의 작업환경을 고려하여 수행되어야 할 것으로 보인다. 따라서 국내에서도 해외문헌을 통해 소개되고 있는 측정센서를 활용하여 마모량을 산출하기 위한 기술을 개발하기 위해서는 독자적인 연구를 통한 시험결과가 요구되는 것으로 보인다.
또한 TBM 디스크커터가 위치하는 커터헤드 내부는 센서를 설치하기에 공간이 매우 협소하며, 전원을 공급하거나 데이터를 전송하기 위한 배선을 작업하는 것이 매우 제한적이다. 따라서 센서의 설치환경, 데이터 전송 등 현장여건에 맞추어 결정해야 할 중요 고려사항들이 존재하므로 이에 대한 자체적인 기술개발이 필요할 것으로 판단되었다.